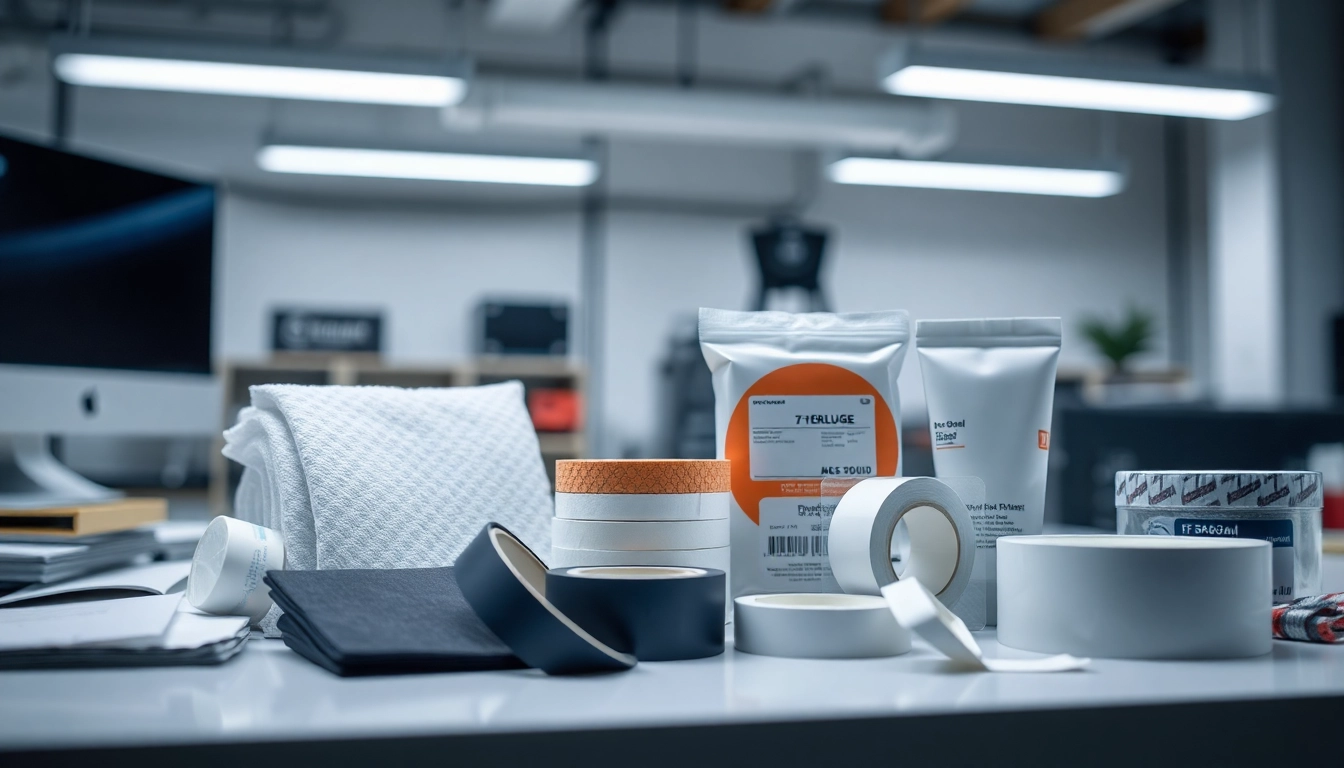
Essential Thermal Management Materials to Enhance Electronic Performance and Reliability
Understanding Thermal Management Materials
What Are Thermal Management Materials?
Thermal management materials refer to a diverse range of products designed to effectively manage, dissipate, and control heat in various applications, particularly in electronics. These materials play a crucial role in enhancing device performance and longevity by optimizing heat flow and reducing thermal resistance. By implementing suitable thermal management strategies, engineers can ensure that electronic components operate within their designated temperature ranges, preventing overheating and subsequent failure.
From thermal interface materials (TIMs) to gap fillers, thermal management materials can take various forms and compositions. They are engineered to enhance thermal conductivity between components, such as semiconductors and heat sinks, thereby ensuring efficient heat transfer. These materials are pivotal in applications ranging from consumer electronics to industrial machinery, significantly impacting device efficiency, reliability, and safety.
An overview of thermal management materials reveals a landscape filled with innovations aimed at addressing the complexities of modern electronic design. By understanding these materials, stakeholders can make informed decisions about their applications and performance metrics.
Importance in Electronics
The role of thermal management materials in electronics cannot be overstated. With the increasing miniaturization of components and heightened performance demands, managing heat dissipation has become a critical consideration in electronic design. Excessive heat can lead to device failures, reduced efficiency, and shortened lifespan. Hence, efficient thermal management is not merely an enhancement; it is essential for the functionality and durability of electronic devices.
Consider the example of smartphones, where compactness and performance compete with thermal demands. Efficient thermal management keeps the device cool, enhancing battery life and user experience. Likewise, in high-performance computing, data centers require highly efficient thermal solutions to ensure optimal component performance and reliability while minimizing energy consumption.
Types of Thermal Management Materials
Thermal management materials can be classified into several categories based on their properties and applications:
- Thermal Interface Materials (TIMs): Designed to fill gaps between heat generating components and heat spreaders or sinks to enhance thermal transfer.
- Thermal Insulation: Materials that prevent heat transfer, used in various applications to maintain temperature.
- Phase Change Materials (PCMs): These absorb or release heat as they change phases (e.g., solid to liquid), helping to stabilize temperatures.
- Thermal Adhesives: Provide structural support while improving thermal contact.
- Gap Fillers: Soft, pliable materials that fill irregular surfaces and enhance thermal conductivity.
Key Applications of Thermal Management Materials
Consumer Electronics
The consumer electronics industry has been at the forefront of employing advanced thermal management materials to enhance product design and efficiency. Devices such as laptops, smartphones, and tablets generate significant heat during operation, necessitating robust thermal management solutions.
For instance, laptop manufacturers utilize a combination of TIMs, thermal pads, and heat spreaders to ensure that CPU and GPU temperatures remain within safe operational limits. As a result, users experience improved performance without the risk of overheating, allowing manufacturers to market devices with high processing capabilities and sleek designs.
Industrial Equipment
In industrial settings, thermal management materials are critical for ensuring machinery and equipment operate efficiently. Heavy machinery, motors, and power electronics generate considerable heat, which can affect operational efficiency and safety. Therefore, manufacturers rely on TIMs, thermal greases, and phase change materials to facilitate effective heat dissipation.
For example, in power electronics, thermal interface materials are used between transistors and heat sinks to improve performance and reliability. Additionally, manufacturers may use thermal insulation materials around sensitive components to maintain thermal stability, enhancing both efficiency and safety in operation.
Aerospace and Automotive
The aerospace and automotive industries face unique challenges regarding thermal management due to their operational environments. In aerospace applications, materials must withstand extreme temperatures and vibrations while maintaining high thermal conductivity. Thermal interface materials and gap fillers are commonly used in avionics and propulsion systems to ensure that critical components operate reliably under challenging conditions.
Similarly, in the automotive sector, effective thermal management is essential for battery systems, especially in electric vehicles. Engineers employ thermal management materials to optimize battery temperature, thereby improving performance, safety, and lifespan. Automotive manufacturers are actively investing in thermal management innovations to meet demanding regulatory standards and consumer expectations.
Choosing the Right Thermal Management Materials
Factors to Consider
Selecting the appropriate thermal management materials is a decision that requires careful consideration of various factors:
- Thermal Conductivity: The ability of a material to conduct heat is paramount. Materials with higher thermal conductivity provide better heat transfer capabilities.
- Viscosity: The viscosity of thermal adhesives and greases affects their application. A lower viscosity often allows for better filling of gaps.
- Mechanical Properties: Depending on the application, the mechanical strength and flexibility of the material may be significant.
- Temperature Stability: Materials should maintain performance across the expected temperature range.
- Application Method: The ease of application (e.g., spreading, dispensing) can influence material selection.
Comparative Analysis of Products
A comparative analysis of different thermal management materials is essential for making informed choices. This involves evaluating performance metrics such as thermal conductivity, thermal resistance, and durability under varying conditions. By conducting performance comparisons and case studies, designers can assess the suitability of various materials for their specific applications.
For instance, comparing TIMs made from silicone versus those made from advanced compounds reveals significant differences in thermal performance, application ease, and cost. Similarly, evaluating different gap fillers and their compliance properties can help ensure an optimal fit for varied surfaces and assemblies.
Cost vs. Performance Trade-offs
When selecting thermal management materials, there is often a trade-off between cost and performance. High-performing materials may come with increased costs, necessitating a careful consideration of budget constraints versus operational efficacy. While low-cost materials may be tempting, they can lead to higher maintenance costs or reduced efficacy in critical applications.
In many cases, investing in higher-quality thermal management materials can yield significant long-term benefits, including enhanced performance, lower failure rates, and increased device lifespan. Thus, manufacturers must evaluate the specific application requirements and potential implications of their material choices on overall product quality and reliability.
Best Practices for Implementing Thermal Management Solutions
Installation Techniques
The success of thermal management solutions hinges significantly on proper installation techniques. Mishandling during installation can lead to improper thermal contact, increasing thermal resistance and jeopardizing system performance.
Best practices include ensuring surface cleanliness, applying appropriate pressure during installation, and using uniform thickness for thermal materials. Additionally, understanding the curing times and temperature profiles for adhesives and compounds is crucial to achieving optimal performance.
Testing and Validation
After installation, thorough testing and validation are crucial to ascertain the effectiveness of thermal management materials. Several methods can be employed, including thermal imaging, which provides visual representations of temperature distributions, and thermocouple measurements that offer precise temperature readings. Conducting these tests allows engineers to identify hotspots and assess whether heat dissipation meets performance criteria.
Maintenance Tips
Once thermal management solutions are implemented, ongoing maintenance is essential to ensure continued performance. This involves regular inspections for signs of wear, degradation, or changes in thermal performance. Components should be monitored for any indications of thermal failure, such as increases in operating temperatures or reduced performance.
Educating maintenance teams on the importance of thermal management and enabling easy access to critical components can promote proactive maintenance, ensuring reliability and longevity.
Future Trends in Thermal Management Materials
Advancements in Material Science
As the demand for more efficient and effective thermal management solutions grows, advancements in material science are at the forefront of innovation. Researchers are exploring new compounds, nanomaterials, and composites to enhance thermal conductivity and performance.
Emerging materials such as graphene and carbon nanotubes promise unprecedented thermal conductivity and mechanical capabilities. These innovations could revolutionize how thermal management solutions are approached across industries.
Eco-friendly Alternatives
As concerns about sustainability gain traction, manufacturers are turning towards eco-friendly alternatives in thermal management materials. The development of bio-based materials and recyclable composites is a growing trend, offering performance benefits while minimizing environmental impact.
Companies are increasingly pressured to adopt more sustainable practices, including reducing waste and developing materials that have a lower carbon footprint. These eco-friendly innovations not only fulfill regulatory requirements but also align with consumer preferences for greener products.
Market Predictions and Growth Areas
The thermal management materials market is expected to grow significantly in the coming years, driven by the rapid advancement of technology and increasing demand across various sectors. Growth areas include electric vehicles, renewable energy systems, and consumer electronics.
The drive for efficiency and sustainability is likely to continue pushing innovations in thermal management, leading to new developments that optimize performance while minimizing costs and environmental impact. Stakeholders who adapt to these changes will likely gain competitive advantages in their respective markets.