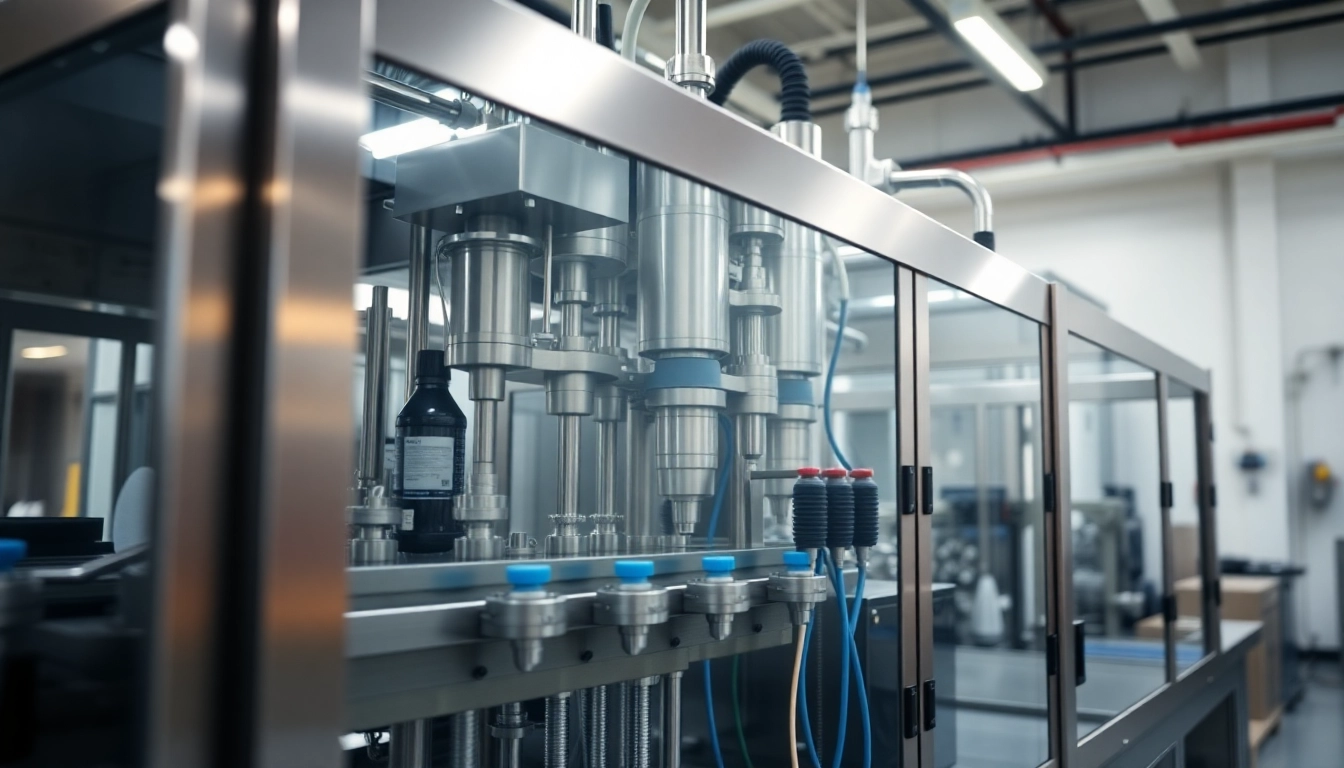
Enhance Your Production Line with Reliable Filling Machine Supplier Solutions
Understanding Filling Machines
What is a Filling Machine?
A filling machine is an automated or semi-automated device used in various industries to fill containers with products like liquids, powders, and granules. These machines enhance the efficiency and accuracy of the filling process, significantly reducing human error and labor costs. In sectors such as food and beverage, pharmaceuticals, cosmetics, and chemicals, filling machines are essential for ensuring product consistency and meeting production timelines.
Types of Filling Machines Available
Filling machines come in various types, each designed to cater to specific product characteristics and packaging needs. Common types of filling machines include:
- Liquid Filling Machines: Ideal for beverages, oils, and chemicals. These machines can operate using piston, pump, gravity, or vacuum filling methods.
- Powder Filling Machines: Designed for filling powdery substances such as spices, flour, and detergents. They often incorporate augers or volumetric fillers.
- Granule Filling Machines: Used for products like sugar, rice, and seeds and are often based on volumetric systems.
- Viscous Filling Machines: Suitable for thicker products such as creams and gels, these machines utilize specialized pumps to handle high viscosity.
- Counter Pressure Filling Machines: Often used for carbonated beverages to prevent foaming during the filling process.
Benefits of Using Filling Machines in Production
The incorporation of filling machines into production lines offers numerous advantages:
- Increased Efficiency: Automated filling systems reduce filling time per container, allowing for faster production rates.
- Consistency and Accuracy: Filling machines can maintain high standards for product volume and weight, ensuring uniformity across batches.
- Labor Cost Reduction: By minimizing the need for manual labor, companies can significantly lower operational costs.
- Scalability: With various machine sizes and configurations available, businesses can scale up production capacity as needed.
- Improved Hygiene: Automated systems are generally more hygienic than manual processes, which is crucial in food and pharmaceutical industries.
Choosing the Right Filling Machine Supplier
Key Features to Look For
When selecting a Filling Machine Supplier, various features should be assessed:
- Technological Expertise: A supplier should have the latest technological advancements in filling machine design and operation.
- Customization Options: Look for suppliers that offer machines tailored to specific product needs and industry requirements.
- Quality Assurance: Suppliers should provide comprehensive quality control measures, including adherence to industry standards and certifications.
- After-Sales Support: Reliable and responsive customer support for maintenance, parts, and upgrades is crucial.
- Experience: Consider suppliers with a proven track record and extensive experience in the field.
Preparing for Supplier Meetings
Preparation is key when meeting potential filling machine suppliers. Consider the following steps:
- Define Your Requirements: Clearly outline your production needs, including the type of product, container sizes, and expected output rates.
- Research Potential Suppliers: Investigate their reputation, customer reviews, and the industries they serve.
- Prepare Questions: Develop a list of questions that address important considerations such as pricing, delivery times, warranty, and training services.
- Request Proposals: Engage multiple suppliers to obtain proposals for comparison, focusing on costs, machine specifications, and support services.
Evaluating Industry Standards
Understanding and evaluating industry standards is paramount in ensuring compliance and quality assurance. Key factors include:
- Regulatory Compliance: Make sure the supplier adheres to relevant local and international regulations, which can affect industries like pharmaceuticals and food safety.
- ISO Certifications: Suppliers should ideally have ISO certifications, demonstrating their commitment to quality management systems.
- Safety Standards: Review safety protocols and standards that the machines adhere to, ensuring a safe working environment.
Common Applications of Filling Machines
Filling Machines in Food and Beverage
In the food and beverage industry, filling machines play a crucial role in processing and packaging. They are used for filling containers with liquids such as juices, sauces, oils, and carbonated drinks. The ability of these machines to maintain hygiene standards and integrate with high-speed production lines makes them essential for meeting consumer demand and adhering to strict health regulations.
Cosmetics and Chemical Industries
Filling machines also serve the cosmetics and chemical industries, where precise filling is critical. From lotions and shampoos to industrial chemicals, products vary in viscosity and require specific filling technology to ensure accuracy and minimize waste. Automated filling machines can help maintain consistency in product quality while keeping production lines efficient.
Pharmaceutical Applications
In pharmaceutical environments, filling machines must comply with stringent regulatory requirements. These machines are vital for filling vials, syringes, and other containers with medications. The use of automated filling systems significantly reduces contamination risks and ensures accurate dosages, critical in the healthcare sector.
Maintenance and Support from Your Supplier
Routine Maintenance Practices
Regular maintenance of filling machines is essential to ensure their long-term performance. Best practices include:
- Scheduled Inspections: Routine check-ups can help identify potential issues before they become severe, ensuring smooth operation.
- Cleaning Protocols: Implementing effective cleaning protocols is crucial, especially in industries like food and pharma, to maintain hygiene.
- Calibration and Testing: Regular calibration ensures that filling accuracy is maintained. Testing the equipment under operational conditions can also highlight any performance issues.
Supplier Support Options
Reliable suppliers should offer robust support options. These typically include:
- Training Programs: Training for your staff on optimal machine operation and maintenance practices enhances efficiency.
- Customer Support: An accessible customer support team can assist with troubleshooting and operational guidance.
- Spare Parts Availability: Suppliers should guarantee easy access to spare parts to minimize downtime during repairs.
Upgrading Your Existing Machines
As technology advances, upgrading existing filling machines can enhance operational efficiency. Consider the following steps when contemplating upgrades:
- Assess Current Equipment: Evaluate the performance of your current machines to identify areas for improvement.
- Consult Suppliers: Engage with your supplier to discuss the latest technologies and enhancements available for your machines.
- Budget Considerations: Prepare a budget that encompasses the cost of upgrades, installation, and potential downtime during transitions.
Future Trends in Filling Machine Technology
Automation and Smart Technology
The future of filling machines is heavily influenced by automation and smart technology. Implementing smart sensors and IoT connectivity allows real-time monitoring of the filling process, enabling operators to optimize productivity, reduce errors, and enhance quality control. Automated systems can adapt to changes in production demands quickly and without significant manual input, promoting efficiency and responsiveness.
Sustainability in Production
With growing environmental concerns, many manufacturers are moving towards sustainable practices. This includes energy-efficient filling machines and the use of eco-friendly materials in both machine construction and packaging. Innovations such as reduced waste in filling processes and recycling initiatives are key trends for manufacturers focusing on sustainability.
The Impact of AI on Filling Processes
Artificial Intelligence (AI) is poised to revolutionize filling processes. Machine learning algorithms can analyze production data to predict maintenance needs, optimize filling processes, and reduce wastage. Moreover, AI can facilitate better demand forecasting, allowing companies to adjust their production schedules accordingly, improving efficiency and resource allocation.