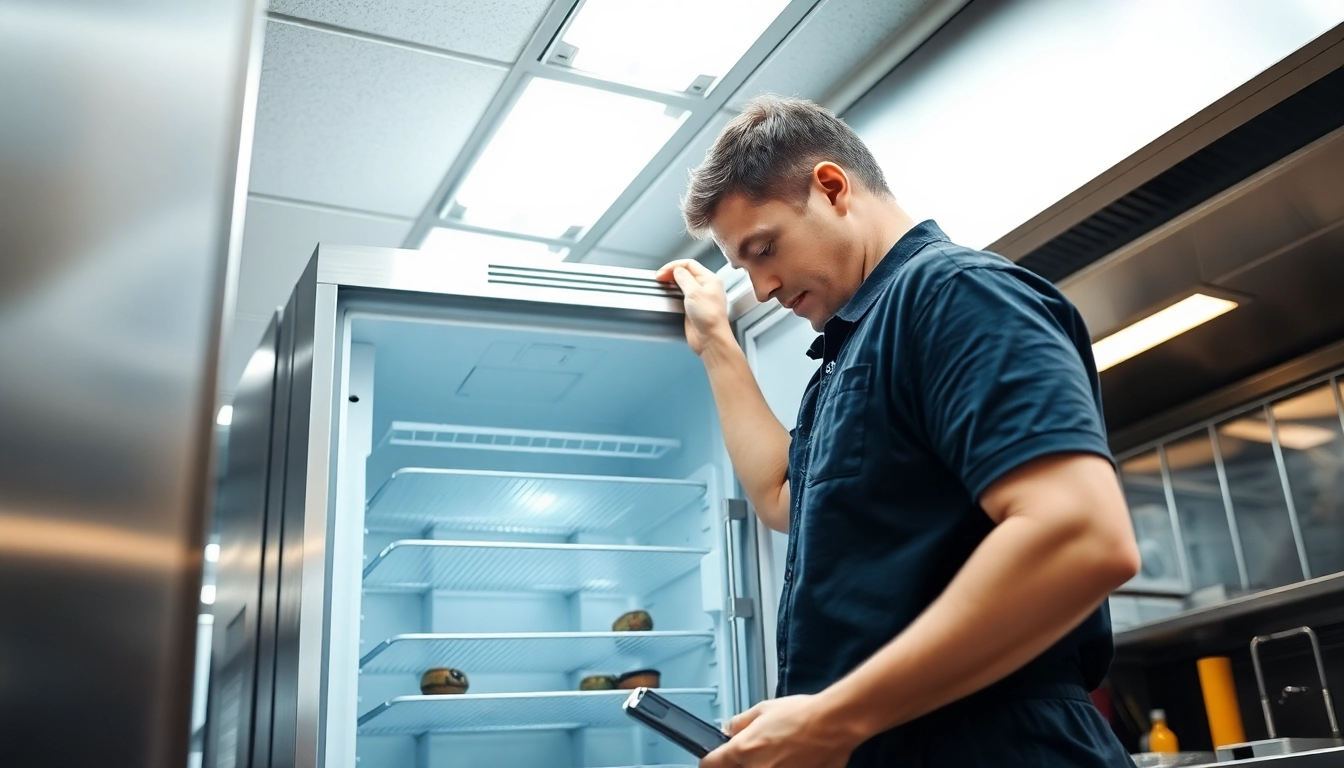
Comprehensive Guide to Commercial Refrigerator Repair for Businesses
Understanding Commercial Refrigerators
Commercial refrigerators are essential units in various businesses, from restaurants and cafes to grocery stores and food manufacturing facilities. They keep perishable goods fresh and safe for consumption, which is crucial in maintaining quality and compliance with health regulations. Therefore, having a well-functioning commercial refrigerator is not only a matter of preserving food but also impacts a business’s overall success.
When it comes to commercial refrigerator repair, understanding the different types, common issues, and maintenance practices is vital for effective troubleshooting and prolonging the lifespan of these units.
Types of Commercial Refrigerators
Commercial refrigerators are designed in various configurations to suit different business needs. Understanding the types can help in pinpointing potential issues and repair strategies:
- Reach-in Refrigerators: Common in restaurants, these units allow easy access to contents. They often have glass doors for visibility and are designed to maintain a consistent temperature.
- Walk-in Coolers: Larger and suitable for bulk food storage, walk-in coolers are essential for grocery stores and larger restaurants. They require specific maintenance and repair techniques due to their size and complexity.
- Beverage Coolers: Used primarily in bars and convenience stores, these specialized units keep drinks at optimal temperatures and have different cooling requirements.
- Freezers: Many operations demand freezers to store products long-term. These, too, come in various sizes and configurations and require specific repair knowledge based on their design.
Common Issues Faced by Businesses
While each type of commercial refrigerator has its benefits, they also come with common issues that can disrupt operations:
- Temperature Fluctuations: Inconsistent temperatures can indicate issues with the thermostat, refrigerant levels, or electrical components.
- Unusual Noises: Strange sounds might point to malfunctioning fans, compressors, or other mechanical components that require immediate attention.
- Loud Operation: Excessive noise can not only be distracting but may signal mechanical distress or a need for maintenance.
- Leaking Water: Condensation buildup can be a sign of clogged drain lines or defective door seals.
Importance of Regular Maintenance
Regular maintenance is crucial in preventing major breakdowns and prolonging the lifespan of commercial refrigerators. Scheduled maintenance can help identify problems before they escalate, ensuring the efficiency of the unit. Key maintenance practices include:
- Cleansing condenser coils to allow efficient heat exchange.
- Checking and replacing door gaskets to prevent air leaks.
- Monitoring refrigerant levels to ensure the cooling system operates effectively.
Signs Your Commercial Refrigerator Needs Repair
Every business owner needs to be aware of the signs indicating that their commercial refrigerator requires repair. Recognizing these symptoms early can save a lot of time and money.
Temperature Fluctuations
Fluctuating temperatures can jeopardize food safety. If you notice that stored items are freezing when they shouldn’t be or are warm, it points towards a malfunctioning cooling system. This can stem from a variety of issues, including:
- A faulty thermostat that does not accurately communicate with the cooling system.
- Blocked air vents that restrict the airflow necessary for even temperature distribution.
Unusual Sounds from the Unit
Commercial refrigerators should operate quietly and efficiently. If you hear loud buzzing, clanging, or grinding, it could indicate:
- Failing components such as fans, motors, or compressors.
- Loose parts that require tightening or replacement.
Food Spoilage and Safety Risks
Ultimately, the most crucial sign of a failing commercial refrigerator is food spoilage. Foods can spoil due to:
- Improper temperature maintenance caused by system failures.
- Inadequate cooling from a blocked condenser or malfunctioning compressor.
Constantly spoiled food not only causes losses but can also pose serious health risks to customers, prompting the need for immediate repair.
Expert Strategies for Quick Repair
When your commercial refrigerator shows signs of trouble, having an effective strategy can help speed up repair processes, minimize downtime, and restore functionality.
Enhancing Diagnostic Techniques
Effective diagnostics begin with correctly identifying the symptoms. Here’s how to enhance the process:
- Document the symptoms before contacting repair professionals to provide them with necessary information.
- Utilize diagnostic tools such as thermometers, multimeters, and pressure gauges to pinpoint issues accurately.
Step-by-Step Repair Processes
Once a diagnosis is established, a structured approach to repair can streamline the process:
- Turn Off the Unit: Always turn off the power supply before beginning repairs.
- Remove Obstructions: Clear away any blocked vents or debris that may be affecting airflow.
- Replace or Repair Parts: Depending on diagnostic results, proceed to repair or replace faulty components.
- Test the Unit: After repairs, monitor the unit’s operation for consistency in temperature and performance.
When to Call a Professional
Not every issue can be resolved with basic troubleshooting. Calling a professional is advisable under circumstances such as:
- Ongoing problems after repairs.
- Complex issues related to electrical or refrigerant systems.
- When the equipment is under warranty, attempting DIY repairs may void coverage.
Prevention Tips for Longevity
Preventative measures can greatly reduce the frequency and severity of repairs. Implementing a few best practices can ensure your commercial refrigerator functions effectively for years.
Regular Cleaning Practices
Cleaning the unit regularly is essential to maintaining its performance:
- Wipe down shelves and the interior regularly to prevent bacteria growth.
- Keep the exterior clean to allow proper airflow to the condenser coils.
Effective Temperature Monitoring
Regularly monitoring temperature can help identify problems before they escalate:
- Use reliable temperature sensors to track fluctuations.
- Set up alerts for any temperature deviations from the norm.
Scheduled Professional Inspections
Routine professional inspections can catch potential issues before they become costly repairs:
- Set schedules for inspections at least twice a year.
- Ensure that all parts of the refrigeration unit are evaluated, including compressors and fans.
Cost Considerations in Commercial Refrigerator Repair
While costs can vary significantly based on multiple factors including the type of repair and root issue, understanding expected expenses can help businesses budget effectively.
Expected Repair Costs
The costs associated with commercial refrigerator repairs can range widely. Typically, service calls average between $150 and $200, with hourly rates from about $45 to $120 based on the technician’s experience and your location. Here are some common repair costs you might encounter:
- Replacing a compressor can cost between $500 and $1,500.
- Thermostat replacements typically range between $200 and $300.
- Repairing or replacing door seals can run $100 to $200.
DIY vs. Professional Services
While exploring DIY repairs can save costs, it’s crucial to weigh the risks against the potential benefits:
- Minor issues like replacing light bulbs or cleaning coils might be safely undertaken by business owners.
- However, complex repairs involving electrical components or refrigerants may require professional expertise to avoid safety hazards or further damage.
Budgeting for Unexpected Repairs
Every business should anticipate the likelihood of unexpected repairs. Implementing a budgeting plan can prepare for these instances:
- Set aside approximately 1–3% of the unit’s purchase price each year for maintenance and repairs.
- Keep an emergency fund specifically for appliance repairs to cover unforeseen issues without straining operational budgets.