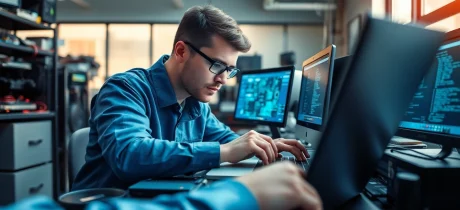
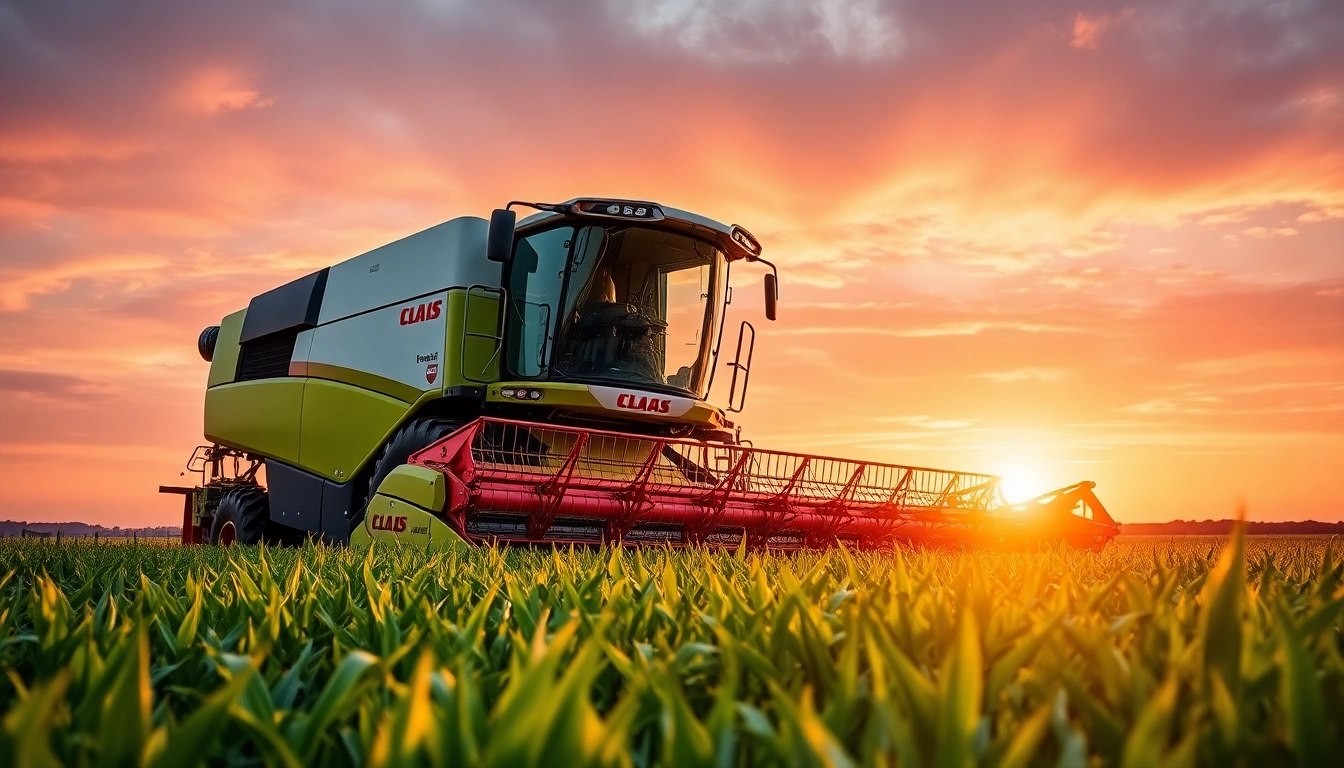
Claas: Führend in der Landwirtschaftstechnik und Maschinenproduktion
Einführung in die Marke Claas
In der Welt der landwirtschaftlichen Maschinen ist Claas ein Begriff, der für Qualität, Innovation und Zuverlässigkeit steht. Gegründet im Jahr 1913 von August Claas, hat sich das Unternehmen seither zu einem der führenden Hersteller von landwirtschaftlichen Maschinen entwickelt. Mit Hauptsitz in Harsewinkel, Nordrhein-Westfalen, stellt Claas eine breite Palette von Geräten her, die Landwirten helfen, ihre Erträge zu maximieren und nachhaltige Praktiken zu fördern. Von modernen Mähdreschern bis hin zu hochentwickelten Traktoren ist Claas ein Synonym für Effizienz in der Landwirtschaft. Für weitere Informationen können Sie die offizielle Claas-Website besuchen.
Geschichte und Gründung von Claas
Die Geschichte von Claas begann vor über einem Jahrhundert. August Claas, der Gründer des Unternehmens, begann seine Karriere mit der Entwicklung des ersten Mähdreschers im Jahr 1913. Seitdem hat Claas kontinuierlich in Forschung und Entwicklung investiert, um innovative Maschinen zu produzieren, die den sich wandelnden Anforderungen der Landwirtschaft entsprechen. Die Einführung des speziellen Mähdreschers, der eine Kombination aus Erntetechnologie und einfacher Bedienbarkeit darstellt, revolutionierte die Art und Weise, wie Getreide geerntet wird.
Im Laufe der Jahre hat sich das Unternehmen global weiterentwickelt, mit zahlreichen internationalen Tochtergesellschaften und Produktionsstandorten, was Claas zu einem der führenden Akteure im Bereich landwirtschaftlicher Maschinen macht. Aktuell beschäftigt Claas weltweit über 11.000 Mitarbeiter und erzielte im Jahr 2023 einen Umsatz von 6,145 Milliarden Euro.
Produkte und Dienstleistungen von Claas
Die Produktpalette von Claas umfasst eine Vielzahl von Maschinen und Geräten, die für verschiedene landwirtschaftliche Anwendungen bestimmt sind. Dazu gehören:
- Mähdrescher
- Traktoren
- Wendewagen
- Ballenpressen
- Ausstattungen für die Präzisionslandwirtschaft
Das Unternehmen bietet darüber hinaus umfassende Dienstleistungen an, darunter Wartung, Beratung und Schulungen für die Benutzer der Maschinen. Dies ist besonders wichtig in einem Bereich, in dem komplexe Technologien oft den Unterschied zwischen Erfolg und Misserfolg ausmachen können.
Marktforschung und Positionierung von Claas
Claas investiert kontinuierlich in Marktforschung, um die Bedürfnisse und Anforderungen der Landwirte besser zu verstehen. Durch Umfragen, Feedback-Sitzungen und die Analyse von Markttrends kann Claas die Entwicklung seiner Produkte präzise steuern. Die Positionierung des Unternehmens auf dem Markt beruht nicht nur auf der Qualität seiner Maschinen, sondern auch auf der Verfügbarkeit von umfassendem Support und einer engen Zusammenarbeit mit den Kunden.
Claas Produkte und ihre Anwendung
Die Bedeutung von Claas Mähdreschern
Claas Mähdrescher sind in der Landwirtschaft äußerst geschätzt. Diese Maschinen sind für ihre Effizienz und Langlebigkeit bekannt. Sie sind mit modernster Technologie ausgestattet, die es den Landwirten ermöglicht, ihre Ernte in kürzester Zeit zu einem optimalen Preis zu sammeln. Die innovativen Systeme zur Ernteüberwachung und -steuerung helfen Landwirten nicht nur, ihre Ernte genau zu verfolgen, sondern auch, ihre Ressourcen effizient zu verwalten.
Traktoren von Claas und ihre Vorteile
Die Traktoren von Claas sind eine weitere Säule des Unternehmens, die für ihre Vielseitigkeit und Stärke geschätzt werden. Sie sind in verschiedenen Größen und Konfigurationen erhältlich, sodass sie für eine Vielzahl von Anwendungen geeignet sind, von der Bodenbearbeitung bis zum Transport. Dank ihrer hohen Leistung und Robustheit sind Claas Traktoren für die anspruchsvollsten landwirtschaftlichen Aufgaben konzipiert und bieten den Landwirten die Zuverlässigkeit, die sie benötigen.
Zusatzgeräte und Technologien von Claas
Claas bietet auch eine Reihe von Zusatzgeräten an, die die Funktionalität ihrer Hauptprodukte erweitern. Dazu gehören Pflüge, Fräsen, Saatmaschinen und Futterernter. Darüber hinaus investiert Claas in intelligente Technologien wie GPS-gesteuerte Systeme und Präzisionslandwirtschaft, um die Effizienz und Produktivität in der Landwirtschaft weiter zu steigern.
Technologische Innovationen bei Claas
Intelligente Landwirtschaft mit Claas
Die intelligente Landwirtschaft ist ein zukunftsweisendes Konzept, das Claas in seinen Produkten integriert. Durch die Verwendung von Sensoren, Datenanalyse und Automatisierungstechnik können Landwirte präzisere Entscheidungen treffen, was zu einer effizienteren Nutzung von Ressourcen führt und die Erträge steigert. Claas hat eine Reihe von Softwarelösungen entwickelt, die Landwirten helfen, ihre Felder effektiv zu verwalten und sofortige Informationen über den Zustand ihrer Maschinen bereitzustellen.
Forschung und Entwicklung im Unternehmen
Die Forschung und Entwicklung (F&E) spielen eine zentrale Rolle im Innovationsprozess von Claas. Das Unternehmen investiert kontinuierlich in neue Technologien und Materialien, um sicherzustellen, dass seine Maschinen den höchsten Standards entsprechen. F&E-Teams arbeiten eng mit Landwirten zusammen, um praktische Lösungen zu entwickeln, die auf realen Herausforderungen basieren.
Nachhaltigkeit und Umweltstrategien von Claas
In einer Zeit, in der die Umweltbelange immer wichtiger werden, hat Claas Nachhaltigkeit zu einer Kernstrategie erklärt. Das Unternehmen verfolgt verschiedene Ansätze zur Minimierung seiner Umweltbelastung, darunter die Entwicklung energieeffizienter Maschinen und die Nutzung erneuerbarer Energien in der Produktion. Außerdem engagiert sich Claas für Initiativen zur Erhaltung der Biodiversität in landwirtschaftlich genutzten Gebieten.
Kundenerfahrungen und Testimonials
Erfahrungsberichte von Landwirten
Die Meinungen und Erfahrungen der Landwirte sind entscheidend für die Weiterentwicklung der Produkte von Claas. Viele Anwender berichten von ihrer positiven Erfahrung mit Claas Maschinen, die nicht nur die Effizienz ihrer Arbeit erheblich erhöhen, sondern auch den Komfort während des Betriebs verbessern. Erfahrungsberichte belegen, dass Landwirte durch den Einsatz von Claas Technologie Zeit und Geld sparen konnten.
Vergleich mit Wettbewerbern
Im Vergleich zu anderen Herstellern hebt sich Claas durch die Kombination aus innovativer Technik, Benutzerfreundlichkeit und einem umfassenden Serviceangebot ab. Wettbewerber wie John Deere und New Holland bieten ebenfalls starke Produkte an, jedoch berichten viele Landwirte, dass Claas eine überlegene Kundenbetreuung und spezifische Anpassungsoptionen bereitstellt, die auf lokale Bedürfnisse eingehen.
Support und Kundendienst von Claas
Die Unterstützung durch Claas endet nicht mit dem Verkauf. Das Unternehmen bietet umfangreiche Schulungsangebote und Techniksupport, um sicherzustellen, dass die Landwirte das Beste aus ihrer Ausrüstung herausholen. Der Kundendienst von Claas wird häufig gelobt und gilt als einer der besten in der Branche, was die langfristige Beziehung zwischen dem Unternehmen und seinen Nutzern stärkt.
Markttrends und zukünftige Entwicklungen
Aktuelle Trends in der Landwirtschaftstechnik
Die Landwirtschaft befindet sich im Wandel, und Technologien wie Automatisierung, Robotik und nachhaltige Praktiken gewinnen an Bedeutung. Claas ist bestrebt, diese Trends zu integrieren und Lösungen anzubieten, die den Landwirten helfen, ihren Betrieb zu optimieren und gleichzeitig die Umwelt zu schonen.
Zukunft von Claas in der globalen Maschinenindustrie
Mit einem klaren Fokus auf Innovation und Nachhaltigkeit ist Claas gut positioniert, um in der sich schnell verändernden globalen Maschinenindustrie weiterhin eine Führungsrolle zu übernehmen. Die fortlaufenden Investitionen in Forschung und Entwicklung sowie die Erschließung neuer Märkte bieten vielversprechende Perspektiven für die Zukunft des Unternehmens.
Schlussfolgerungen und Empfehlungen für Landwirte
Für Landwirte, die nach Lösungen suchen, um ihre Effizienz zu steigern und ihre landwirtschaftlichen Praktiken zu verbessern, bietet Claas eine Vielzahl von Optionen an, die auf Qualität und neuesten Technologien basieren. Eine Investition in Claas Maschinen kann nicht nur zu einer höheren Produktivität führen, sondern auch helfen, nachhaltigere Praktiken in die tägliche Arbeit zu integrieren. Das Unternehmen bleibt ein vertrauenswürdiger Partner für die Landwirtschaft und unterstützt Landwirte bei der Erreichung ihrer Ziele.
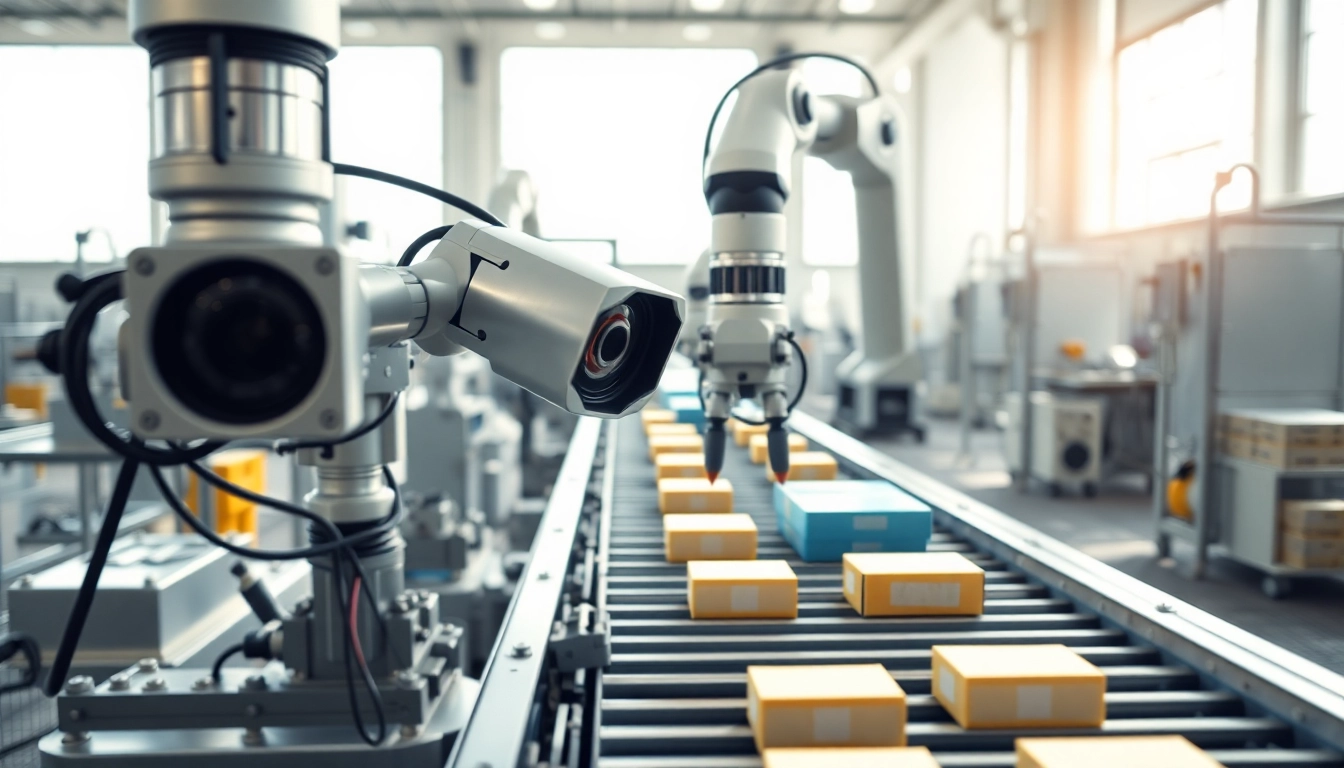
The Essential Guide to Machine Vision: Applications and Technologies
Understanding Machine Vision
With the rapid advancement of technology, industries are harnessing state-of-the-art tools to enhance efficiency and accuracy. One such powerful tool is machine vision, which incorporates computer algorithms to help machines interpret visual data in real-time. This technology is not just a matter of seeing but involves a comprehensive system to analyze images, detect defects, and make informed decisions—revolutionizing sectors from manufacturing to healthcare.
What is Machine Vision?
Machine vision refers to the ability of a computer system to interpret and understand visual information from the world, leveraging imaging technology. It encompasses the acquisition of images, processing the captured data, and executing tasks based on this interpretation. Unlike human vision, which is deeply influenced by perception and context, machine vision relies on pre-programmed algorithms and artificial intelligence to carry out specific functions.
The Role of Cameras and Sensors
Cameras are the centerpiece of machine vision systems, capturing images that provide the raw data for analysis. Various types of cameras can be utilized, ranging from standard visible light cameras to specialized devices like infrared or color cameras. Coupled with sensors, these cameras can provide vital information about products on an assembly line, detect anomalies, or even assess the integrity of components. The choice of camera and sensor significantly impacts the quality and reliability of the image data captured, making it crucial to select the appropriate technology for specific applications.
Comparison: Machine Vision vs. Computer Vision
Although the terms ‘machine vision’ and ‘computer vision’ are often used interchangeably, it’s essential to understand their differences. Machine vision is primarily focused on using visual data for specific applications, mainly in industrial settings, where the goal is often automation and defect detection. On the other hand, computer vision encompasses a broader scope, including the development of algorithms that allow machines to interpret visual data from everyday environments, supporting applications like facial recognition and autonomous navigation.
Applications of Machine Vision
Machine vision technology has found its place across various fields due to its flexibility and effectiveness. Below, we explore some of the critical applications of machine vision in contemporary settings.
Quality Control in Manufacturing
One of the most prominent applications of machine vision is in quality control during manufacturing processes. The ability to consistently monitor products as they move through production lines ensures that only those meeting specific standards proceed to the next step. For instance, in the automotive industry, machine vision systems can identify defects such as scratches or dents on vehicle surfaces before assembly, reducing costly recalls.
Furthermore, real-time data captured through machine vision allows manufacturers to maintain detailed records of quality inspections, enabling better decision-making and improvements in the production process.
Automation in Warehousing
With the rise of e-commerce, warehousing operations have seen intensified demands for speed and accuracy. Machine vision facilitates automation by allowing systems to identify, categorize, and sort items efficiently. For example, optical barcode scanners, powered by machine vision, enable rapid processing of goods as they arrive in warehouses, reducing manual errors and significantly speeding up inventory management.
Moreover, advanced robotics equipped with machine vision capabilities can navigate complex warehouse layouts, perform tasks like picking and packing with precision, enhancing overall operational efficiency.
Healthcare Uses and Innovations
In the healthcare sector, machine vision technology plays an essential role in diagnostics and surgical assistance. High-resolution imaging systems are utilized in radiology to analyze medical images and detect anomalies, such as tumors or fractures. Applications extend to robotic-assisted surgeries, where machine vision systems guide surgical tools with precision, improving patient outcomes while reducing recovery times.
Additionally, machine vision can aid in clinical laboratories by automating the image analysis process, allowing for quicker diagnoses and more accurate patient data management.
Components of Machine Vision Systems
A machine vision system is composed of various components that work together to capture and interpret visual information. Understanding these components is vital for anyone looking to implement machine vision into their operations.
Cameras and Optical Systems
Cameras form the backbone of machine vision systems. Depending on the application, different camera types can be employed, such as CCD (Charge-Coupled Device) or CMOS (Complementary Metal-Oxide-Semiconductor) cameras. Optical systems, including lenses and filters, also significantly influence image quality. High-quality lenses ensure that cameras capture clear, sharp images, while specialized filters can enhance specific wavelengths of light, improving analysis accuracy.
Lighting Techniques for Optimal Imaging
Lighting plays a crucial role in machine vision systems, as poorly lit images can lead to inaccurate analyses. Various lighting techniques may be employed, including backlighting, sidelighting, or diffuse lighting to emphasize relevant features in the image. For instance, backlighting can be beneficial for detecting edges or contours, while diffuse lighting minimizes shadows and allows for a more uniform illumination of surfaces. Engineers must design appropriate lighting setups specific to the tasks at hand to maximize data capture quality.
Processing Hardware and Software Algorithms
After images are captured, they require processing to yield useful insights. The processing component involves dedicated hardware, such as GPUs (Graphics Processing Units) or FPGAs (Field Programmable Gate Arrays), which optimize computational speed for complex analyses. Software algorithms, including machine learning techniques, enhance a system’s ability to analyze datasets, detect patterns, and apply classification. The integration of robust processing hardware with efficient algorithms determines a machine vision system’s performance and reliability.
Implementing a Machine Vision Solution
The path to successfully implementing a machine vision solution requires careful planning and execution. Here are the critical steps and considerations involved in this process.
Steps for System Integration
- Define the Application Goals: Begin by clearly delineating what you wish to achieve with machine vision. Whether it’s quality assurance, product sorting, or defect detection, understanding objectives will guide your choices.
- Select Appropriate Components: Based on your application goals, choose cameras, sensors, lighting, and software tools suited to your specific environment and tasks.
- Install and Calibrate Systems: Carefully install the chosen components and calibrate them to work together seamlessly. Calibration ensures that all elements are aligned and operational, fine-tuning the setup for robustness.
- Testing and Validation: Conduct trials to validate the system’s functionality and performance, ensuring effectiveness in fulfilling the intended application goals.
- Continuous Monitoring and Optimization: Once implemented, consistently monitor system performance and seek opportunities for improvements based on evolving needs and technological advancements.
Common Challenges and Solutions
While implementing machine vision solutions can yield significant benefits, several challenges may arise:
- Image Quality Issues: Poor image quality can hamper analysis. To address this, invest in high-quality cameras and optimize lighting conditions.
- System Integration Difficulties: Compatibility issues between hardware and software components may occur. Confirm that all selected components are designed to work in conjunction with one another.
- High Initial Costs: The upfront investment in machine vision technology can be substantial. Balance this by evaluating the long-term savings and efficiency gains that machine vision can facilitate.
Performance Metrics to Consider
To measure the effectiveness of a machine vision system accurately, it’s essential to track several performance metrics, including:
- Image Processing Speed: The time taken to capture and analyze images should be minimized to ensure real-time applications.
- Accuracy and Precision: Evaluate the percentage of correct detections and classifications against total instances to assess reliability.
- System Uptime: Ensure minimal disruptions in operations due to downtime, as high uptime is a desirable outcome for any automation process.
Future Trends in Machine Vision
As technology continues to evolve, so will the capabilities and applications of machine vision. Understanding these future trends is vital for organizations looking to remain competitive.
Advancements in Artificial Intelligence
The integration of artificial intelligence (AI) into machine vision systems is set to transform the landscape dramatically. AI algorithms can enhance the capability of these systems, enabling them to learn from data patterns and adapt over time. For instance, deep learning methods allow for improved object recognition and classification, even in complex environments.
As AI technology matures, the potential for autonomous decision-making through machine vision will increase, leading to more sophisticated applications across various industries.
Market Growth and Industry Forecasts
The machine vision industry is poised for substantial growth, with projections reflecting a multibillion-dollar global market by the end of the decade. Various sectors, including manufacturing, logistics, healthcare, and automotive, are expected to fuel demand due to the increasing need for automation and quality assurance processes.
Investments in machine vision technology can lead to substantial efficiency improvements, making it a focal point for companies looking to upgrade their operations.
The Impact of Machine Vision on Automation
As machine vision continues to integrate with robotics and AI, its impact on automation will be profound. The ability for systems to interpret and act upon visual information in real-time paves the way for greater automation in industries ranging from production lines to grocery stores. This shift toward automation promises increased efficiency, cost savings, and enhanced product quality, representing a significant transformation in operational paradigms.
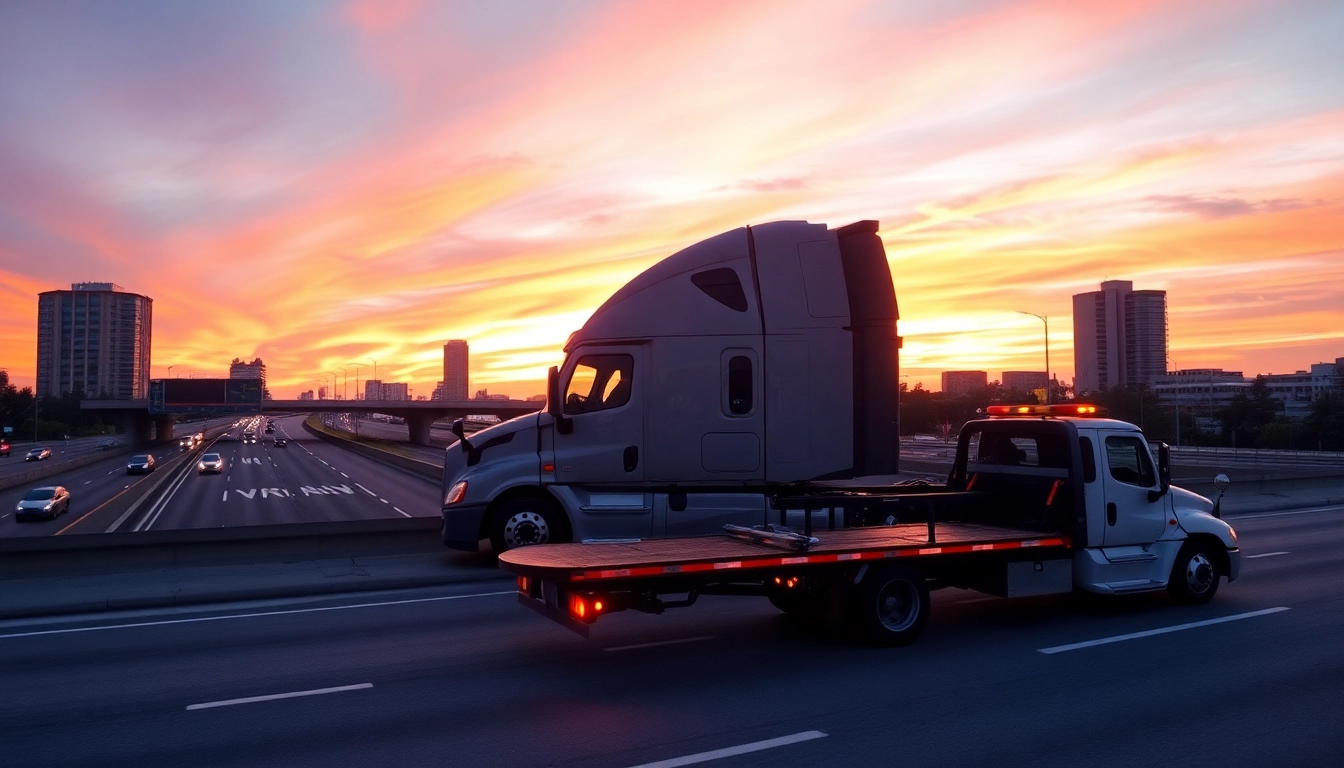
Reliable Semi-Truck Towing in Tampa: Fast and Professional Services
Understanding Semi-Truck Towing Needs in Tampa
When it comes to the logistics and transportation industry, semi-trucks play a vital role in delivering goods and services efficiently. However, the unpredictable nature of road travel means that breakdowns and emergencies can occur at any moment. In Tampa, understanding the specific needs associated with semi-truck towing Tampa services is crucial for truck owners. Whether you’re dealing with a mechanical failure or an accident, knowing what services are available at your disposal can save time, money, and stress.
Common Reasons for Semi-Truck Towing
Semi-trucks are massive machines that endure rigorous conditions. Common reasons requiring towing services include:
- Mechanical Failures: Engine problems, transmission issues, or electrical failures can leave a truck immobilized.
- Accidents: Collisions with other vehicles, or unexpected road conditions can necessitate immediate towing.
- Punctured Tires: A flat tire on a semi-truck can be particularly challenging to replace on the road.
- Fuel Issues: Running out of fuel or using the wrong type can lead to serious operational problems.
Emergency Towing Services Explained
Emergency towing services are specifically designed to respond promptly to urgent situations. In Tampa, several towing companies offer 24/7 services, equipped to handle the unique demands of heavy-duty trucks. These companies have the necessary trucks, equipment, and trained personnel to tackle any situation efficiently. Understanding how these emergency services work is crucial:
- Rapid Response Times: Reliable towing services can rapidly arrive at your location to minimize downtime.
- Specialized Equipment: Equipment like heavy-duty wreckers and tilt beds are employed to accommodate large vehicles.
- Safety Protocols: Professional tow operators follow strict safety guidelines to ensure that both the truck and the crew remain unharmed during the towing process.
Choosing a Reliable Towing Service
Selecting a dependable towing service is critical. Factors to consider include:
- Reputation: Look for companies with a positive track record and solid online reviews.
- Certifications: Ensure that the towing company is licensed, insured, and uses trained personnel.
- Availability: The best companies offer round-the-clock services, ensuring you are covered at any time of day.
- Cost Transparency: Request a breakdown of the costs involved—including service fees, mileage, and any additional charges to avoid surprises later.
Top Features of Professional Semi-Truck Towing Services
24/7 Availability and Response Time
In the transportation industry, time is money, and when a truck breaks down, it can lead to expensive delays. Professional semi-truck towing services in Tampa offer 24/7 availability meaning they can respond to your emergencies any time of the day or night. This availability is essential for minimizing downtime and ensuring that your goods are delivered on time.
Equipment and Technology in Towing
Semi-truck towing requires specialized equipment to safely facilitate the towing process. This equipment includes:
- Heavy-Duty Tow Trucks: These vehicles are specifically designed to handle the weight and size of semi-trucks.
- Flatbed Trailers: Often used for towing trucks that may have significant damage or complications preventing them from being towed in the traditional manner.
- Winches and Load Binders: These assist in securing the truck during towing to prevent further damage.
Customer Support and Communication
Effective customer support is a hallmark of quality towing services. Operators should provide clear communication regarding estimated arrival times, costs, and the towing process. Customers should feel confident that their vehicles are in good hands and have their questions answered promptly.
Comparative Analysis of Towing Providers in Tampa
Overview of Competitors in the Area
The landscape of semi-truck towing services in Tampa features numerous providers with varying offerings. Some of the top contenders include:
- B&D Towing & Recovery: Known for their 24-hour heavy truck towing and commercial services across Tampa Bay.
- Sunstate Wrecker: Offers comprehensive heavy-duty towing solutions and boasts a highly-rated service within the metro area.
- TIA Towing: Provides emergency towing services and has a solid reputation in handling heavy-duty vehicles.
Service Price and Quality Comparisons
Pricing structures can vary widely between towing companies based on factors such as distance, type of service required, and the specific equipment used. It’s advisable to compare quotes from multiple providers while also considering the quality of service. The lowest price may not always equate to the best service, so weigh the pros and cons carefully.
User Testimonials and Ratings
User reviews and testimonials can provide vital insights into the reliability and quality of service offered by towing companies. Websites like Google Business, Yelp, and specialized towing service reviews can help you get a clearer picture of the experiences other customers have had.
Benefits of Choosing Local Tampa Towing Services
Familiarity with Local Roads and Regulations
Local towing companies possess extensive knowledge of Tampa’s roadways, traffic patterns, and local regulations. This familiarity allows them to navigate to your location quickly and efficiently, reducing wait times during emergencies.
Community Trust and Support
Selecting a local service also means supporting the community. Local towing companies often rely on their reputation, which drives them to provide superior service to maintain trust within the community. They are more likely to go above and beyond to keep their customers satisfied.
Fast Response Times for Local Clients
Local companies can typically respond faster thanks to their proximity. This advantage is crucial during emergencies where every minute counts. They can often reach stranded vehicles quicker than larger, national chains that may take longer to dispatch help.
How to Prepare for a Towing Service Call
Information to Have Ready for the Towing Company
Before calling for a towing service, having pertinent information ready can expedite the process significantly:
- Location: Provide an accurate address or description of where the truck is situated.
- Type of Vehicle: Specify that it’s a semi-truck, including make and model if possible.
- Nature of the Problem: Describe any known issues or accidents leading to the need for towing.
Safety Precautions During a Breakdown
Safety should always be a priority during breakdowns. Here are a few precautionary measures:
- Move to a Safe Location: If possible, drive the truck to a nearby safe spot away from traffic.
- Use Hazard Lights: Turn on your hazard lights to alert other drivers of your situation.
- Stay Inside the Vehicle: Unless it’s unsafe to do so, stay inside your truck until help arrives.
Post-Towing Procedures for Truck Owners
After your semi-truck has been towed, there are essential steps to follow to ensure its proper recovery:
- Assessment: Conduct a thorough inspection of the truck for any additional damages.
- Contact a Mechanic: Schedule a mechanic visit to identify and fix the issues causing the breakdown.
- Review Towing Expenses: Understand the towing bill and ensure it aligns with prior estimates.
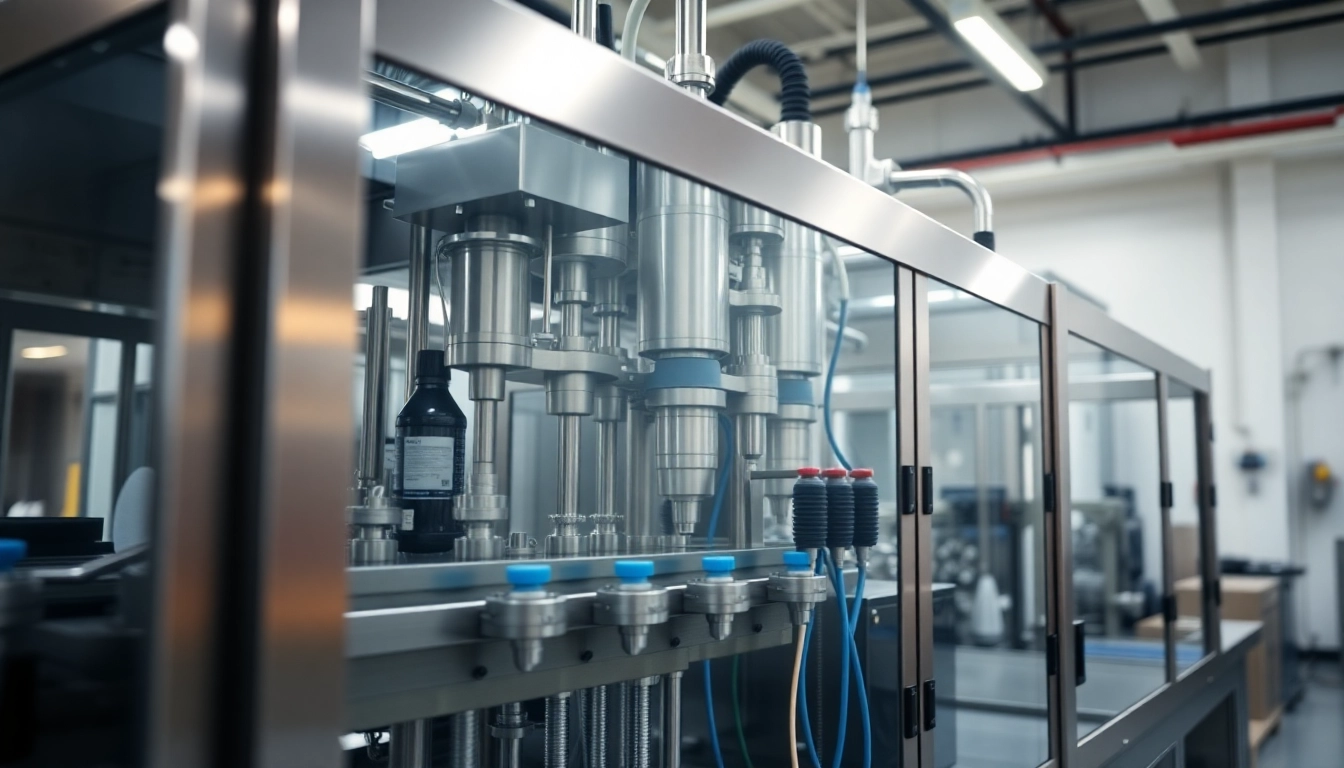
Enhance Your Production Line with Reliable Filling Machine Supplier Solutions
Understanding Filling Machines
What is a Filling Machine?
A filling machine is an automated or semi-automated device used in various industries to fill containers with products like liquids, powders, and granules. These machines enhance the efficiency and accuracy of the filling process, significantly reducing human error and labor costs. In sectors such as food and beverage, pharmaceuticals, cosmetics, and chemicals, filling machines are essential for ensuring product consistency and meeting production timelines.
Types of Filling Machines Available
Filling machines come in various types, each designed to cater to specific product characteristics and packaging needs. Common types of filling machines include:
- Liquid Filling Machines: Ideal for beverages, oils, and chemicals. These machines can operate using piston, pump, gravity, or vacuum filling methods.
- Powder Filling Machines: Designed for filling powdery substances such as spices, flour, and detergents. They often incorporate augers or volumetric fillers.
- Granule Filling Machines: Used for products like sugar, rice, and seeds and are often based on volumetric systems.
- Viscous Filling Machines: Suitable for thicker products such as creams and gels, these machines utilize specialized pumps to handle high viscosity.
- Counter Pressure Filling Machines: Often used for carbonated beverages to prevent foaming during the filling process.
Benefits of Using Filling Machines in Production
The incorporation of filling machines into production lines offers numerous advantages:
- Increased Efficiency: Automated filling systems reduce filling time per container, allowing for faster production rates.
- Consistency and Accuracy: Filling machines can maintain high standards for product volume and weight, ensuring uniformity across batches.
- Labor Cost Reduction: By minimizing the need for manual labor, companies can significantly lower operational costs.
- Scalability: With various machine sizes and configurations available, businesses can scale up production capacity as needed.
- Improved Hygiene: Automated systems are generally more hygienic than manual processes, which is crucial in food and pharmaceutical industries.
Choosing the Right Filling Machine Supplier
Key Features to Look For
When selecting a Filling Machine Supplier, various features should be assessed:
- Technological Expertise: A supplier should have the latest technological advancements in filling machine design and operation.
- Customization Options: Look for suppliers that offer machines tailored to specific product needs and industry requirements.
- Quality Assurance: Suppliers should provide comprehensive quality control measures, including adherence to industry standards and certifications.
- After-Sales Support: Reliable and responsive customer support for maintenance, parts, and upgrades is crucial.
- Experience: Consider suppliers with a proven track record and extensive experience in the field.
Preparing for Supplier Meetings
Preparation is key when meeting potential filling machine suppliers. Consider the following steps:
- Define Your Requirements: Clearly outline your production needs, including the type of product, container sizes, and expected output rates.
- Research Potential Suppliers: Investigate their reputation, customer reviews, and the industries they serve.
- Prepare Questions: Develop a list of questions that address important considerations such as pricing, delivery times, warranty, and training services.
- Request Proposals: Engage multiple suppliers to obtain proposals for comparison, focusing on costs, machine specifications, and support services.
Evaluating Industry Standards
Understanding and evaluating industry standards is paramount in ensuring compliance and quality assurance. Key factors include:
- Regulatory Compliance: Make sure the supplier adheres to relevant local and international regulations, which can affect industries like pharmaceuticals and food safety.
- ISO Certifications: Suppliers should ideally have ISO certifications, demonstrating their commitment to quality management systems.
- Safety Standards: Review safety protocols and standards that the machines adhere to, ensuring a safe working environment.
Common Applications of Filling Machines
Filling Machines in Food and Beverage
In the food and beverage industry, filling machines play a crucial role in processing and packaging. They are used for filling containers with liquids such as juices, sauces, oils, and carbonated drinks. The ability of these machines to maintain hygiene standards and integrate with high-speed production lines makes them essential for meeting consumer demand and adhering to strict health regulations.
Cosmetics and Chemical Industries
Filling machines also serve the cosmetics and chemical industries, where precise filling is critical. From lotions and shampoos to industrial chemicals, products vary in viscosity and require specific filling technology to ensure accuracy and minimize waste. Automated filling machines can help maintain consistency in product quality while keeping production lines efficient.
Pharmaceutical Applications
In pharmaceutical environments, filling machines must comply with stringent regulatory requirements. These machines are vital for filling vials, syringes, and other containers with medications. The use of automated filling systems significantly reduces contamination risks and ensures accurate dosages, critical in the healthcare sector.
Maintenance and Support from Your Supplier
Routine Maintenance Practices
Regular maintenance of filling machines is essential to ensure their long-term performance. Best practices include:
- Scheduled Inspections: Routine check-ups can help identify potential issues before they become severe, ensuring smooth operation.
- Cleaning Protocols: Implementing effective cleaning protocols is crucial, especially in industries like food and pharma, to maintain hygiene.
- Calibration and Testing: Regular calibration ensures that filling accuracy is maintained. Testing the equipment under operational conditions can also highlight any performance issues.
Supplier Support Options
Reliable suppliers should offer robust support options. These typically include:
- Training Programs: Training for your staff on optimal machine operation and maintenance practices enhances efficiency.
- Customer Support: An accessible customer support team can assist with troubleshooting and operational guidance.
- Spare Parts Availability: Suppliers should guarantee easy access to spare parts to minimize downtime during repairs.
Upgrading Your Existing Machines
As technology advances, upgrading existing filling machines can enhance operational efficiency. Consider the following steps when contemplating upgrades:
- Assess Current Equipment: Evaluate the performance of your current machines to identify areas for improvement.
- Consult Suppliers: Engage with your supplier to discuss the latest technologies and enhancements available for your machines.
- Budget Considerations: Prepare a budget that encompasses the cost of upgrades, installation, and potential downtime during transitions.
Future Trends in Filling Machine Technology
Automation and Smart Technology
The future of filling machines is heavily influenced by automation and smart technology. Implementing smart sensors and IoT connectivity allows real-time monitoring of the filling process, enabling operators to optimize productivity, reduce errors, and enhance quality control. Automated systems can adapt to changes in production demands quickly and without significant manual input, promoting efficiency and responsiveness.
Sustainability in Production
With growing environmental concerns, many manufacturers are moving towards sustainable practices. This includes energy-efficient filling machines and the use of eco-friendly materials in both machine construction and packaging. Innovations such as reduced waste in filling processes and recycling initiatives are key trends for manufacturers focusing on sustainability.
The Impact of AI on Filling Processes
Artificial Intelligence (AI) is poised to revolutionize filling processes. Machine learning algorithms can analyze production data to predict maintenance needs, optimize filling processes, and reduce wastage. Moreover, AI can facilitate better demand forecasting, allowing companies to adjust their production schedules accordingly, improving efficiency and resource allocation.
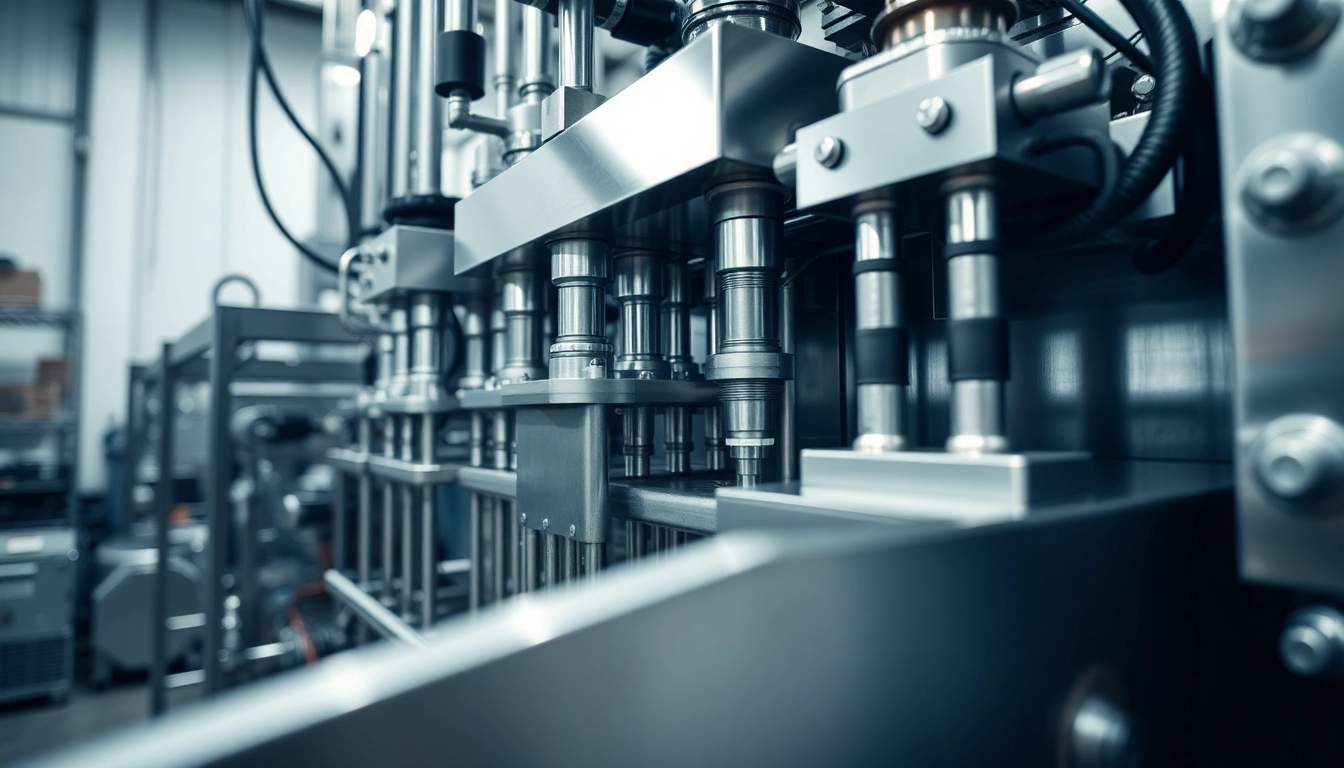
Leading Filling Machine Supplier for Efficient Packaging Solutions
Introduction to Filling Machines
In the world of manufacturing and production, filling machines play a crucial role, enabling businesses to efficiently package their products. These machines are vital across various industries, including food and beverage, pharmaceuticals, cosmetics, and chemicals, streamlining the packaging process and ensuring consistency in the quantity filled. As a prominent Filling Machine Supplier, understanding the intricacies of filling machines can empower businesses to make informed decisions about their packaging needs.
What is a Filling Machine?
A filling machine is a type of equipment used to dispense a predetermined volume or weight of liquid, granule, powder, or solid into a container. They are pivotal in ensuring that products are packaged accurately and efficiently, catering to various sectors ranging from food production to pharmaceutical manufacturing. By utilizing specialized mechanisms, filling machines can maintain hygiene standards, adhere to regulatory requirements, and enhance overall productivity.
Different Types of Filling Machines
Filling machines come in various configurations and types, each designed to meet specific manufacturing needs. The main types include:
- Manual Filling Machines: These require human intervention to fill containers and are generally used for low-volume production.
- Semi-Automatic Filling Machines: Operated with some manual control, these machines increase efficiency and reduce labor costs while still requiring some human oversight.
- Fully Automatic Filling Machines: These machines operate entirely on their own, making them ideal for high-volume production settings. They typically include advanced technology that monitors and controls the filling process.
- Piston Filling Machines: Popular for viscous liquids, these machines utilize pistons to deliver precise amounts of product, ensuring accuracy in each container.
- Pump Filling Machines: Best for thin liquids, these machines utilize pumps to fill containers with speed and efficiency.
- Gravity Filling Machines: Using gravity to fill containers, these are best suited for low-viscosity liquids.
- Vacuum Filling Machines: These machines remove air from the container to preserve product quality, particularly in the food and beverage sector.
Applications of Filling Machines
Filling machines serve various applications across multiple industries:
- Food and Beverage Industry: From juices to sauces and carbonated drinks, filling machines ensure accurate servings while minimizing spills and contamination.
- Pharmaceutical Sector: They are essential for distributing liquids and powder formulations, ensuring medications are dosed accurately for efficacy and safety.
- Cosmetics and Personal Care Products: Filling machines are also used for lotions, creams, and perfumes, requiring precision to maintain product integrity.
- Chemicals: Industrial chemicals often require specialized filling machines to manage hazardous materials safely and efficiently.
Choosing the Right Filling Machine Supplier
Selecting the right filling machine supplier is a critical decision that can significantly impact production efficiency and product quality. Here are key considerations to guide your choice:
Evaluating Supplier Expertise
Assessing a supplier’s expertise in filling technology is essential. Look for suppliers with a proven track record in your industry, as they are more likely to offer machines that cater to your specific needs. Examine their history, types of machines they provide, and the ranges of products they support. Consider reaching out to existing clients for testimonials regarding the supplier’s performance and reliability.
Quality Certification and Standards
Quality certifications such as ISO 9001 can assure you of the supplier’s commitment to maintaining industry standards. Suppliers should comply with relevant regulatory requirements related to safety, hygiene, and operational efficiency, particularly in industries such as food and pharmaceuticals. Request documentation to verify that their machines meet these standards and protocols.
Customer Support and Service
Post-purchase support is a crucial aspect to consider when selecting a supplier. A reliable filling machine supplier should offer comprehensive services, including installation, training, and ongoing maintenance. Evaluate their customer service track record, availability of technical assistance, and access to replacement parts. A responsive support team can minimize downtime and ensure your equipment stays operational.
Benefits of Using Automated Filling Machines
The integration of automated filling machines can yield significant benefits for manufacturing businesses, enhancing efficiency and effectiveness throughout the production line. Some notable advantages include:
Increased Efficiency and Productivity
Automated filling machines drastically reduce the time taken to fill containers, which is especially beneficial in high-demand settings. With minimal human intervention, these machines can operate continuously, increasing production rates and allowing businesses to meet larger volumes of orders promptly.
Precision and Accuracy in Filling
With advanced technology, automated filling machines offer heightened accuracy that manual processes cannot match. This precision minimizes product wastage and ensures that each container is filled to the correct volume, which is vital for compliance in industries like pharmaceuticals and food production.
Cost Savings in the Long Term
Investing in automated filling solutions can lead to significant cost savings over time. Beyond the reduction in labor costs, these machines decrease material wastage, ensuring greater efficiency in operations. While the upfront costs may be higher, the long-term benefits often justify the initial investment.
Innovations in Filling Machine Technology
The evolution of filling machines is marked by technological innovations that enhance their functionality. Staying informed about these trends is essential for businesses aiming to optimize their packaging processes. Notable innovations include:
Smart Technology Integration
Current filling machines increasingly incorporate smart technology, enabling real-time monitoring and data collection. These innovations allow businesses to track production efficiency, detect inconsistencies, and optimize workflows through actionable insights. Features such as IoT integration facilitate predictive maintenance, reducing unplanned downtimes.
Eco-Friendly Solutions in Manufacturing
As sustainability becomes a focal point in manufacturing, many suppliers are developing eco-friendly filling machine solutions. These machines are designed to minimize energy consumption, reduce waste, and utilize sustainable materials in their construction. Manufacturers are also adapting to changing consumer preferences for eco-conscious packaging.
Future Trends in Filling Machines
Industry experts predict several future trends in filling machine technology, including:
- Increased Customization: Tailored solutions that cater to unique manufacturing processes will become more prevalent, allowing businesses to maximize output.
- Enhanced Automation: Future machines will likely integrate AI and machine learning techniques to further streamline operations and increase adaptability in production lines.
- Advanced Cleaning and Safety Features: Innovations in hygiene technology will address increasing health regulations, particularly in food and pharmaceutical industries.
Conclusion: Partnering with a Reliable Filling Machine Supplier
In conclusion, partnering with a reliable filling machine supplier can profoundly impact the packaging efficiency of your business. As you evaluate potential suppliers, consider their expertise, quality certifications, customer support, and technological advancements. Implementing automated filling solutions not only enhances efficiency and accuracy but also positions your business to adapt to future market demands.
Key Takeaways for Businesses
To summarize:
- Filling machines are essential to achieving efficient packaging across various industries.
- Choosing the right supplier is critical; consider their expertise and support services.
- Automation significantly enhances productivity, precision, and cost-efficiency.
Getting Started with Your Supplier
To embark on your journey towards optimizing your filling processes, start by conducting thorough research on potential suppliers. Compile a list of questions regarding their products, services, and support systems. Arrange consultations to discuss your specific requirements, ensuring alignment with your operational goals.
Resources and Further Reading
For additional insights, consider exploring industry-specific forums, webinars, and publications. Engaging with peer discussions can provide valuable perspectives on the latest trends and technologies in filling machine solutions.
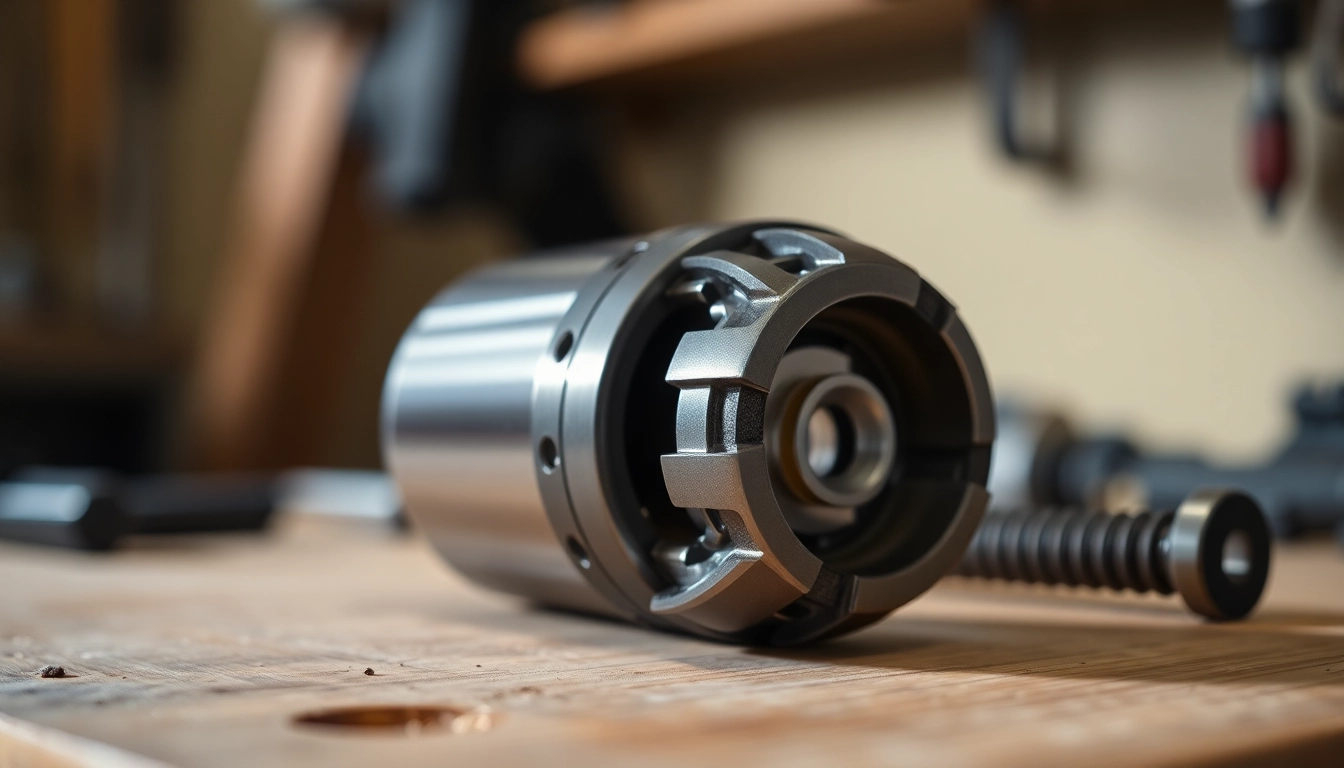
Choosing the Right Drill Chuck: A Guide to Precision and Performance
Understanding Drill Chucks
What is a Drill Chuck?
A drill chuck is a clamping device used to hold drill bits and other cutting tools securely in place on a power drill. This essential component connects the drill bit to the drill’s motor, allowing the power from the drill to be transmitted to the bit, thus enabling it to cut through materials. The performance and reliability of a drill are significantly influenced by the design and quality of the chuck used.
Types of Drill Chucks Explained
There are several types of drill chucks, each serving different purposes depending on the application, types of materials, and the user’s preferences. The most common kinds are:
- Keyed Drill Chucks: These chucks require a key to tighten or loosen the grip on the drill bit. They provide a secure hold, reducing the risk of slipping, which is especially important when working with harder materials.
- Keyless Drill Chucks: As the name suggests, these chucks do not require a key. You can tighten or loosen them by hand, which allows for faster bit changes. They are suitable for light to medium work, where precision isn’t as critical.
- Hybrid Chucks: These combine features from both keyed and keyless chucks. They may allow for quick adjustments while still providing a secure fit.
- Specialized Chucks: Some chucks are designed for specific applications, such as for mini drills, or chucks that adapt to different bit sizes or shapes.
Key Features to Consider
When selecting a drill chuck, there are several key features to assess:
- Capacity: Refer to the maximum and minimum bit sizes the chuck can accommodate, which determines its versatility.
- Material: The chuck material influences durability and performance. Steel or composite materials are typically robust.
- Type of Clamping Mechanism: Whether keyed or keyless, the mechanism should be easy to use and reliable.
- Concentricity: This measures how well the chuck holds the bit. High concentricity is crucial for precision work, as it affects the drill’s accuracy and the quality of the finished holes.
Benefits of High-Quality Drill Chucks
Impact on Drilling Precision
High-quality drill chucks dramatically enhance precision. Accurate hole placement is critical in various industries, from woodworking to metal fabrication. A reliable chuck ensures that the drill bit does not wobble during operation, maintaining a consistent cutting path and producing cleaner, more precise holes.
Durability and Longevity
The materials utilized in the construction of drill chucks significantly impact longevity. Quality chucks made from hardened steel or other durable materials can withstand greater wear and tear. Additionally, they typically have better resistance to rust and corrosion, promoting a longer usable life even under demanding conditions.
Efficiency in Handling
Efficiency is a substantial consideration when using power tools. High-quality drill chucks allow for quicker bit changes, reducing downtime and increasing productivity. Keyless models, in particular, enable users to swiftly swap bits with one hand, which is invaluable when moving between tasks or drill bits frequently.
How to Choose the Right Drill Chuck
Assessing Your Needs
Choosing the right drill chuck begins with assessing your specific needs. Consider the types of projects you typically undertake. If you’re a hobbyist, a keyless chuck may suffice. However, if you require precision work in a professional setting, investing in a high-quality keyed chuck would be prudent. Understanding the frequency of use and the variety of materials encountered will also guide your selection.
Comparing Keyless vs. Keyed Models
When deciding between keyless and keyed drill chucks, think about the trade-offs. Keyless chucks offer convenience and faster bit changes, making them ideal for projects requiring frequent adjustments. In contrast, keyed chucks provide superior clamping strength and precision, which can be essential for tasks demanding high accuracy. Evaluate the nature of your work to select the most suitable option.
Evaluating Size and Compatibility
Not all chucks fit every drill, so ensuring compatibility is vital. Pay attention to both the shank size of your drill bits and the mounting style of the chuck. Common sizes include 1/2 inch and 3/8 inch, but verify the specifications of your power tool to avoid purchasing the wrong chuck. An incompatible chuck can lead to inefficient drilling practices and potential damage to both the chuck and the drill.
Popular Drill Chuck Brands and Models
Top Choices for Professional Use
Professional users often turn to brands renowned for their quality and performance. Some of these include:
- Jacobs: Known for their robust and reliable keyed chucks, Jacobs models are widely used in industrial settings.
- Albrecht: Albrecht chucks are celebrated for their precision and quality, making them a go-to for applications requiring exact specifications.
- Röhm: With a focus on engineering excellence, Röhm provides options that enhance torque and concentricity.
Best Budget Options
For budget-conscious consumers, there are still effective and reliable drill chucks available that don’t compromise performance. Brands such as DEWALT and Bosch offer cost-effective options without sacrificing essential quality features.
Innovative Features in Current Models
Today’s drill chucks are more sophisticated than ever. Recent innovations include:
- Automatic Bit Locking: Some chucks now feature mechanisms that automatically lock the bit in place, enhancing safety during operation.
- Adjustable Torque Settings: Certain models allow users to adjust torque settings directly from the chuck, improving control while drilling.
- Integrated LED Lights: Visibility is improved with built-in lights that illuminate dark work areas, enhancing accuracy while maintaining safety.
Maintenance Tips for Your Drill Chuck
Cleaning and Care Practices
Regular cleaning and maintenance of your drill chuck are crucial for optimal performance. Here are best practices to follow:
- Keep it Dry: Moisture can lead to rust and corrosion. Always store your drill chuck in a dry environment and wipe it down after use.
- Remove Debris: After frequent drilling, debris can accumulate in the chuck. Using a soft brush or cloth can help remove such build-up without damaging its mechanism.
- Lubrication: Periodically oiling the chuck’s mechanism can enhance its functionality and longevity.
Identifying Wear and Tear
Constant usage can lead to signs of wear and tear on drill chucks. Common signs include:
- Difficulty in tightening or loosening the bit
- Wobbling or inconsistent drilling
- Visible damage or scoring on the chuck’s surface
When to Replace Your Drill Chuck
Knowing when to replace your drill chuck is vital for maintaining efficiency and safety. If you notice significant wear, difficulty in bit holding, or excessive wobbling during use, it’s time to consider a replacement. Investing in a high-quality chuck can mean the difference between achieving precise results and dealing with the frustration of poor performance.
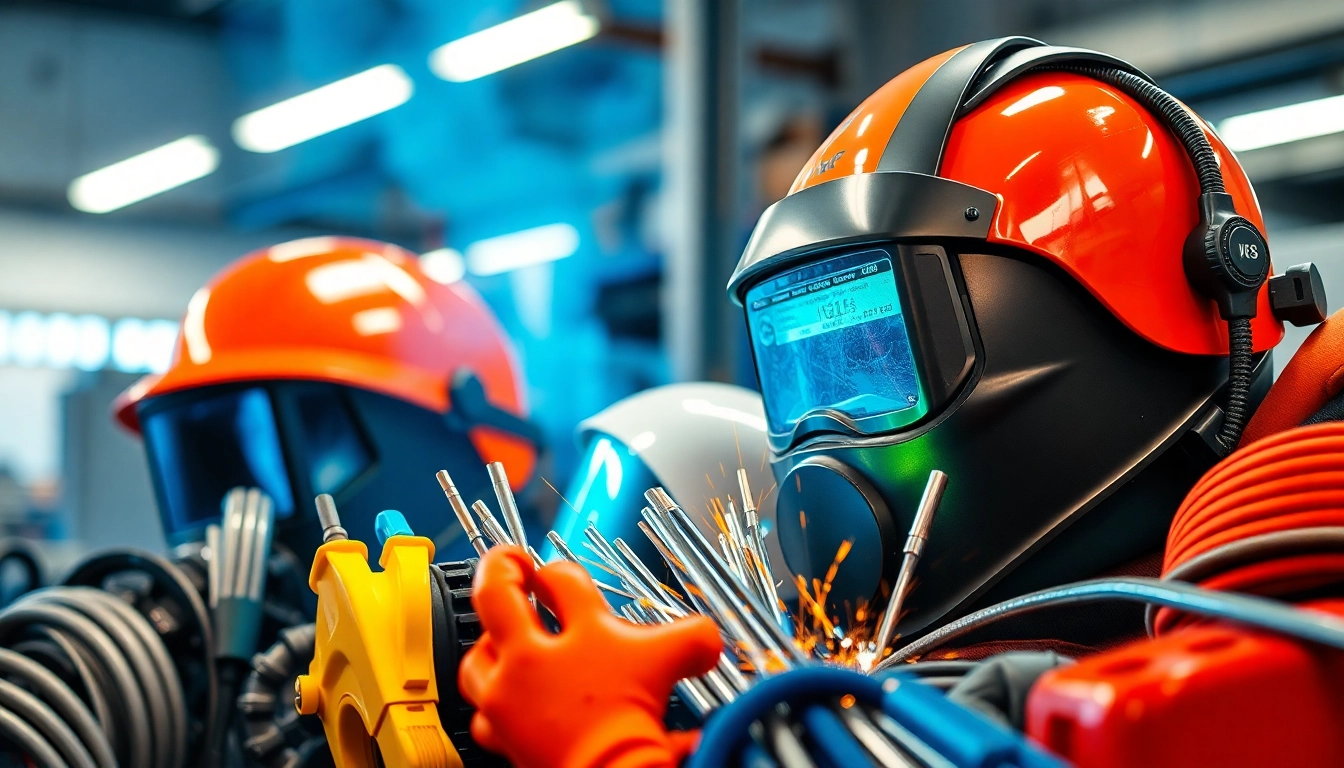
Your Comprehensive Guide to Finding Welding Supplies Near Me
Understanding Welding Supplies
Welding is both an art and a science, fundamental in various industries ranging from construction to manufacturing. To successfully engage in any welding project, a welder requires a range of welding supplies. These supplies can influence the quality, efficiency, and safety of welding jobs. If you’re on the hunt for welding supplies near me, it’s essential to start with a solid understanding of what you need.
Types of Welding Supplies
The spectrum of welding supplies is vast, categorized based on their specific applications and techniques. Here are the main types:
- Welding Machines: This includes MIG (Metal Inert Gas), TIG (Tungsten Inert Gas), and stick welders. Each type serves unique functions and is suitable for different kinds of welding projects.
- Electrodes and Filler Metals: These are essential in the welding process, helping to create strong bonds between the materials being joined.
- Welding Torches: Used primarily with MIG and TIG welding, these torches deliver a concentrated arc for precise melting of metals.
- Protective Gear: Essential safety equipment includes helmets, gloves, and protective clothing to shield welders from sparks and ultraviolet radiation.
- Welding Gases: Often, welding requires gases such as argon, CO2, or acetylene for the process, depending on the method employed.
- Cutting Equipment: Plasma cutters and torches help prepare materials before welding, ensuring clean edges and precise cuts.
Common Uses in Different Industries
Welding supplies play a crucial role across several sectors:
- Construction: Building structures like bridges and skyscrapers involves extensive welding.
- Automotive: Frames, chassis, and components are created and repaired using welding techniques.
- Aerospace: Precision welding is necessary for aircraft components, where safety is paramount.
- Manufacturing: Many products, from machinery to consumer goods, incorporate welding in their assembly processes.
- Artistic Projects: Metalworking artists use welding to create sculptures and installations, showcasing the artistic side of this technique.
Benefits of Quality Welding Supplies
Investing in quality welding supplies yields significant advantages:
- Durability: Quality equipment lasts longer, reducing replacement costs.
- Safety: Reliable gear adds layers of protection, reducing the risk of workplace accidents.
- Efficiency: High-quality tools perform better, allowing for faster and more precise work.
- Weld Strength: The integrity of welds produced with superior materials is superior, making a difference in structural applications.
- Reputation: Professionals using high-quality supplies are likely to gain a better reputation, leading to more business opportunities.
Where to Find Welding Supplies Near Me
Finding the right welding supplies involves considering both local and online options, depending on convenience and availability.
Local Retailers and Supply Shops
Local suppliers often offer the advantage of immediate retrieval. Here are some types of stores to consider:
- Specialized Welding Supply Stores: Establishments focused on welding can provide targeted products and expert advice.
- Hardware Stores: Chains like Home Depot and Lowe’s often carry a variety of welding supplies.
- Industrial Suppliers: These suppliers cater to businesses and might offer bulk supplies at better rates.
Exploring nearby options can provide the benefit of expert staff who can help you choose supplies tailored to your needs.
Online Options for Convenient Shopping
Online shopping has transformed the way welders acquire their supplies. Advantages include:
- Wide Selection: Online platforms typically offer a broader range of products than local stores.
- Price Comparisons: Easily compare prices and find the best deals.
- Home Delivery: Conveniently receive items without leaving home.
However, it’s essential to ensure you’re purchasing from credible websites that specialize in welding supplies to ensure quality.
How to Verify a Supplier’s Credibility
To avoid scams or low-quality products, consider the following methods to verify a supplier:
- Read Reviews: Customer feedback on platforms like Google and Yelp can provide insights into their quality and service.
- Seek Recommendations: Industry connections often have trustworthy suppliers they can recommend.
- Certifications: Check if the supplier meets industry standards and holds necessary certifications.
- Return Policies: Reliable suppliers usually have customer-friendly return or exchange policies.
Comparing Prices: Value for Money
Understanding the prices of welding supplies can help you avoid overspending while ensuring you get the right tools for your projects. Here’s how to approach it.
Average Costs of Common Supplies
The cost of welding supplies can vary significantly based on type, brand, and grade:
- Welding Machines: Prices for basic models start around $300, while professional-grade machines can exceed $5,000.
- Electrodes: A box of electrodes may range from $20 to $100 depending on type and quantity.
- Protective Gear: A quality welding helmet can cost around $50 to several hundred dollars depending on features.
- Gas Cylinders: Acetylene tanks usually cost between $100 and $300 for initial fills, with additional costs for refills.
Discounts and Deals: What to Look For
When purchasing welding supplies, it pays to keep an eye out for deals. Consider these tactics:
- Seasonal Sales: Many suppliers offer discounts during major holidays or specific sales events.
- Bulk Purchasing: Buying supplies in bulk can often lead to significant savings.
- Loyalty Programs: Some suppliers maintain reward systems for frequent customers, providing additional discounts.
Budgeting for Your Welding Needs
A clear budget helps in managing your expenses effectively. Here are some steps to create one:
- List Required Supplies: Identify what tools and materials you need and their estimated costs.
- Prioritize Needs: Categorize your list into essential and optional items.
- Monitor Spending: Keep track of your purchases and adjust your budget as necessary to stay within limits.
Safety Equipment and Practices
Safety in welding is paramount due to the inherent risks involved. Proper protective gear, safety practices, and awareness can prevent accidents and injuries.
Essential Safety Gear for Welders
Investing in quality safety gear is non-negotiable for any welder:
- Welding Helmet: Protects the face and eyes from sparks and harmful radiation.
- Gloves: Fire-resistant gloves help prevent burns and provide grip.
- Protective Clothing: Flame-resistant jackets and pants reduce the risk of serious injuries.
- Respirators: Essential when working with toxic fumes to protect respiratory health.
Best Practices for Safe Welding
In addition to gear, following safety practices is crucial:
- Prepare the Work Area: Ensure the workspace is clear of flammable materials.
- Ventilation: Proper airflow helps dissipate potentially harmful fumes.
- Training: Ensure all personnel are trained in welding safety protocols.
Resources for Welding Safety Training
Several organizations offer training and resources for welders looking to enhance their safety knowledge:
- American Welding Society (AWS) – Offers certification programs and safety guidelines.
- Occupational Safety and Health Administration (OSHA): Provides safety regulations for workplace environments.
- Online Training Platforms: Websites like Coursera and Udemy have courses focused on welding safety.
The Future of Welding Supplies
The welding industry is evolving, influenced by technological advances and shifting market demands. Understanding these trends can prepare you for the future.
Innovations in Welding Technology
Recent years have seen significant advancements in welding technologies:
- Automation: Robotic welding systems improve efficiency and precision in manufacturing.
- 3D Printing: Integrating additive manufacturing with welding techniques opens new avenues for production.
- Digital Monitoring: Innovations allow for real-time monitoring of welding conditions for better quality control.
Trends Impacting Supply Availability
Several trends affect the accessibility and availability of welding supplies:
- Global Supply Chain Challenges: Disruptions can lead to delays in material availability, affecting local suppliers.
- Demand for Sustainable Products: Increasing demand for eco-friendly welding practices may drive changes in how suppliers operate.
- Consumer Preferences: As DIY projects gain popularity, suppliers may see increased demand for smaller quantities of supplies.
Sustainable Welding Practices and Supplies
As sustainability becomes a priority across industries, welding is no exception:
- Recyclable Materials: Utilizing materials that can be recycled helps reduce waste.
- Energy-efficient Equipment: New technologies focus on reducing energy consumption during the welding process.
- Safe Disposal Practices: Implementing proper disposal methods for chemicals and waste materials supports environmental efforts.
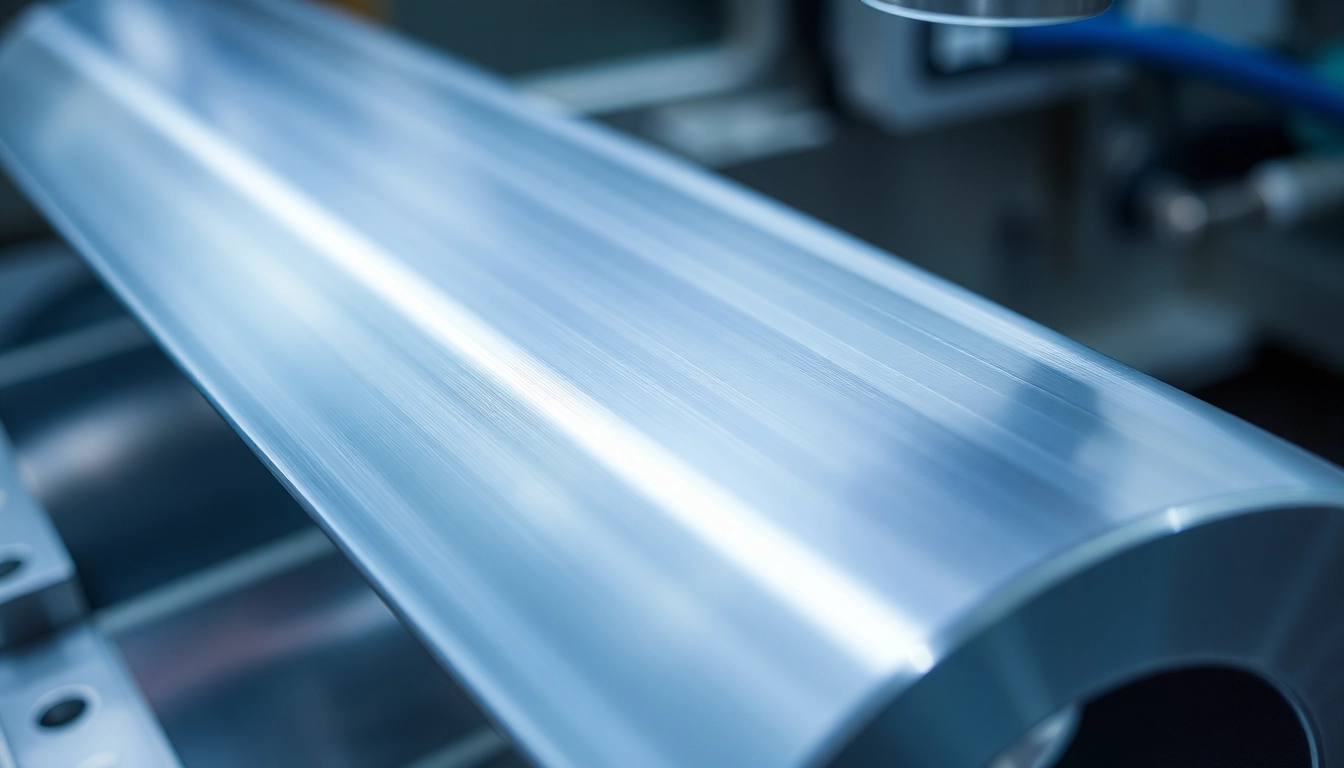
Understanding EP Coating: The Key to Enhanced Corrosion Resistance in metal components
What is EP Coating?
Definition and Overview
EP Coating, commonly known as Electrophoretic Coating or E-Coating, is a sophisticated surface finishing technology widely used across various industries to coat conductive materials. The process involves the use of an electric field to drive charged paint particles onto a substrate, resulting in a uniform and durable coating. This method not only enhances the aesthetic appeal of products but also plays a crucial role in providing corrosion resistance to components made of metals and other conductive substances. By employing techniques that allow for precise adhesion, ep coating has gained popularity in sectors such as automotive, electronics, and industrial machinery.
How EP Coating Works
The mechanism behind electrophoretic coating incorporates principles of electrochemistry and physics. Here’s a step-by-step breakdown of the process:
- Preparation of the Substrate: Initially, the metal surface that requires coating is thoroughly cleaned and pre-treated to remove any contaminants. This step is critical as it ensures the paint adheres well to the surface.
- Creating a Paint Slurry: A specialized paint is mixed with water to form a slurry. The paint is electrically charged, with either positively or negatively charged particles depending on the type of electrophoretic coating being used.
- Electrophoretic Deposition: The substrate is immersed in the paint slurry and is connected to an electrical power source. When the current flows, the paint particles migrate towards the substrate, forming a uniform film.
- Curing: After the desired thickness of the coating is achieved, the substrate is removed from the bath and cured, usually in an oven at elevated temperatures. This step solidifies the coating and enhances its durability.
Common Applications of EP Coating
EP coating is versatile and finds applications across numerous fields. Some of its major uses include:
- Automotive Industry: EP coating is significantly applied to automobile components for rust prevention and aesthetic appeal. It is particularly vital for undercarriage parts that undergo harsh environmental conditions.
- Consumer Electronics: Many electronic devices, including mobile phones and laptops, utilize E-coating to provide a sleek finish while protecting internal components from corrosion.
- Industrial Equipment: Machinery and tools used in industrial settings are often coated with EP to extend their lifespan and reduce maintenance costs.
- Household Appliances: Many household appliances undergo EP coating to ensure a durable finish that withstands regular wear and tear.
Benefits of EP Coating
Corrosion Resistance
One of the most outstanding benefits of EP coating is its exceptional resistance to corrosion. The coating forms a barrier that prevents moisture and other corrosive elements from reaching the substrate beneath. This property is especially crucial for outdoor applications, automotive components, and equipment in high-humidity environments. Studies have shown that parts coated with EP exhibit significantly longer lifespans in corrosive environments compared to untreated surfaces.
Durability and Longevity
EP coatings are known for their durability. Once cured, they can withstand significant wear, impact, and abrasion. The resilience of E-coat ensures that products maintain their appearance over time and do not easily chip or fade. Many manufacturers find that their costs related to products’ maintenance and replacements decrease significantly when utilizing this advanced coating technique.
Environmental Impact and Safety
EP coating processes are designed with environmental considerations in mind. The majority of modern E-coating paints are water-based, which reduces emissions of volatile organic compounds (VOCs). Additionally, the efficiency of the electrophoretic process minimizes waste, as excess paint can often be recovered and reused. This eco-friendly aspect makes EP coating a preferable option for businesses aiming to enhance their sustainability practices.
EP Coating Process Explained
Pre-treatment Steps
Before the actual coating process begins, it is vital to prepare the substrate meticulously. The pre-treatment steps generally include:
- Cleaning: The substrate undergoes thorough cleaning with detergents or solvents to eliminate any oil, grease, or dirt. This is often followed by rinsing with high-pressure water.
- Surface Roughening: In some cases, surfaces may be mechanically abraded or chemically treated to increase their surface area, ensuring a stronger bond with the coating.
- Conversion Coating: Metal phosphating or chromating treatments may be applied to enhance corrosion resistance further.
The Electrophoretic Process
Once pre-treatment is complete, the electrophoretic process is initiated. As mentioned previously, this involves immersing the substrate into the prepared paint slurry and applying an electric current, facilitating the deposition of paint onto the surface. The thickness of the coating can be controlled by adjusting the voltage and duration of the immersion.
Post-Application Curing
The final step in the EP coating process is curing, typically achieved through heat. The substrate is exposed to elevated temperatures, often in an oven, which helps in crosslinking the polymer chains in the coating. This curing step is crucial for enhancing the toughness and chemical resistance of the coating.
Comparing EP Coating with Other Coating Techniques
EP Coating vs. Powder Coating
While both EP coating and powder coating serve similar purposes, they differ significantly in application and properties:
- Application Method: EP coating uses an electrochemical process for painting whereas powder coating applies dry paint particles through an electrostatic charge.
- Finish Quality: EP coats tend to provide a more uniform finish, especially on complex geometries, whereas powder coating may struggle in some tight corners.
- Durability: Both methods result in durable finishes, but EP coatings offer superior corrosion resistance, making them ideal for outdoor applications.
EP Coating vs. Traditional Painting
Traditional painting methods, while widely used, often fail to match the durability of EP coatings. EP coatings can provide a consistent and dense layer impervious to harmful environmental factors, a feat that is more challenging for traditional brush or spray paints to achieve. Additionally, EP coatings reduce overspray and waste, making them more environmentally friendly.
Industry Insights and Trends
Industry experts point out a growing trend towards automated and advanced electrophoretic systems, as manufacturers increasingly seek to optimize production efficiency and reduce costs. Furthermore, as regulatory standards for VOC emissions tighten, the demand for environmentally-friendly coatings, like EP, is expected to rise in line with industry shifts towards sustainability.
Choosing the Right EP Coating Service
Key Considerations
When selecting a service provider for EP coating, several factors must be taken into account:
- Experience and Expertise: Look for providers with a proven track record and extensive experience in the electrophoretic coating process. Their technical knowledge will greatly impact the quality of your coating.
- Equipment and Technology: The latest technology in application and curing should be utilized. Advanced systems can lead to better coating adhesion and uniformity.
- Quality Assurance: Ensure the provider adheres to industry standards and practices, including robust quality control measures throughout the coating process.
Evaluating Service Providers
Choosing the right EP coating service provider requires careful assessment. Potential clients should consider visiting facilities, reviewing case studies, and checking client testimonials to gauge the provider’s capabilities and reputation. Engaging in direct discussions about their processes will also illuminate how well they align with your specific needs.
Cost Factors and Budgeting for EP Coating
Evaluating the cost of EP coating involves understanding several critical factors, including:
- Volume of Production: Higher volumes typically reduce the per-unit cost of coating due to economies of scale.
- Pre-treatment Requirements: Custom pre-treatment procedures may incur additional costs, impacting the overall pricing.
- Finishing and Curing Techniques: The method chosen can influence not just quality but also cost. Opting for a quicker curing can increase costs slightly, but can optimize production timelines.
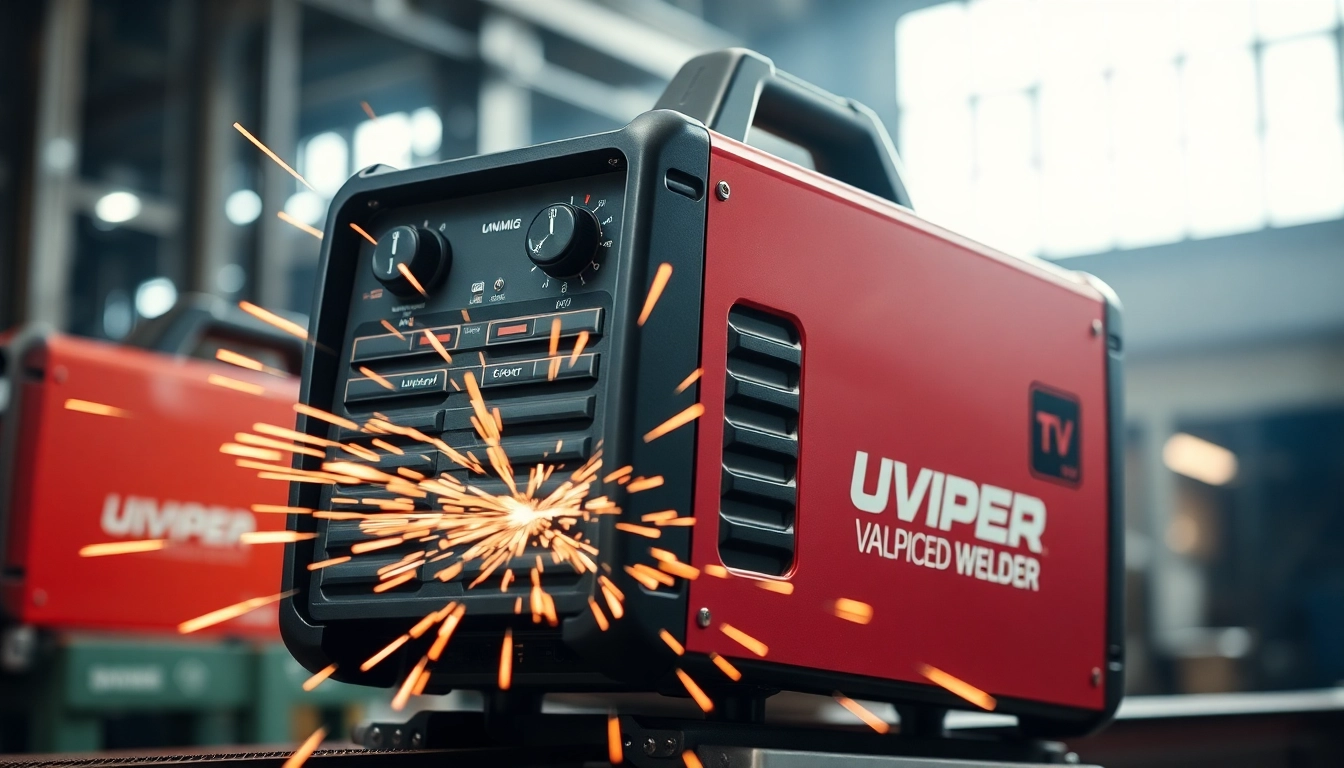
Master Your Welding Projects with the Versatile Unimig Viper Welder
1. Introduction to the Unimig Viper Welder
The world of welding has been revolutionized with the introduction of versatile, multi-process machines, and among them, the Unimig Viper stands out. This welder has gained popularity due to its exceptional capabilities and user-friendly design. If you’re in search of an all-in-one solution for various welding tasks, the unimig viper is an excellent option to consider. It not only caters to different welding methods but also provides impressive performance metrics that appeal to both beginners and seasoned welders alike.
– What is the Unimig Viper?
The Unimig Viper is a multi-process welder that facilitates MIG, TIG, and Stick welding, offering flexibility for a range of projects. Designed to cater to various skill levels, this machine is well-regarded in workshops, industrial environments, and among DIY aficionados. Its compact design and lightweight form factor allow for ease of transport and usability, making it convenient for both fixed and mobile applications.
– Key Features of the Unimig Viper
- Multi-Process Capability: The Unimig Viper simplifies welding with its ability to switch between MIG, TIG, and Stick processes seamlessly.
- User-Friendly Interface: The intuitive controls make it accessible for beginners while still offering advanced settings for experienced welders.
- Portable Design: Weighing relatively little, it’s perfect for on-site projects and small workshops.
- Durability and Reliability: Built to last, the Unimig Viper withstands harsh working conditions without compromising performance.
– Benefits of Multi-Process Welding
The ability to perform multiple welding processes in one machine means users can take on various projects without investing in multiple machines. This not only saves money but also reduces the learning curve associated with each type of welding. Being able to switch between methods quickly means you can tackle everything from fine, delicate tasks to heavy-duty welding.
2. Technical Specifications
– Power and Performance Metrics
The power ratings of the Unimig Viper include a voltage range of 10 – 185 A, making it suitable for both light and heavy-duty applications. Its inverter technology ensures stable performance and high efficiency while consuming less energy. The machine’s output is consistently rated, which allows for effective welding across different materials, including stainless steel, mild steel, and aluminum.
– Welding Capabilities: MIG, TIG, and Stick
Each welding process comes with its own unique applications, and the Unimig Viper excels in all three:
- MIG Welding: Ideal for quick, strong, and easy-to-use welds, particularly in sheet metal work and larger frameworks.
- TIG Welding: Provides precise control, allowing for high-quality welds on thin materials, which is especially beneficial in automotive and aerospace applications.
- Stick Welding: Offers a simpler approach for outdoor welding tasks, as it is less affected by wind and surface cleanliness.
– User-Friendly Interface and Design
The control panel of the Unimig Viper features easy-to-read displays and straightforward dials, allowing users to adjust settings without confusion. Ergonomically designed handles and a lightweight frame enhance maneuverability. Overall, the design prioritizes ease of use, making it an ideal option for users of all experience levels.
3. Application Scenarios
– Home Workshop Use
In a home workshop, the Unimig Viper is invaluable. Whether crafting metal furniture, repairing bikes, or engaging in hobbyist projects, its versatility and efficiency make it the go-to machine. Beginners can rapidly learn the basics, while experienced welders can rely on its performance for precision tasks.
– Industrial Applications
In industrial settings, the Unimig Viper serves vital roles from fabrication to repair tasks. Its robust build and ability to handle different welding processes make it perfect for maintenance on machinery and structural components, enabling diverse applications across industries such as manufacturing, construction, and automotive repair.
– Ideal Projects for Beginners and Experts
Beginners may start with simple projects like brackets and metal art, while experts can take on complex fabrications involving multiple materials and techniques. The adaptability of the Unimig Viper means it remains relevant as users’ skillsets grow over time.
4. Maintenance and Troubleshooting
– Routine Care for Longevity
Keeping the Unimig Viper well-maintained is crucial for long-lasting performance. Routine checks such as inspecting cables for wear, cleaning the nozzle, and ensuring good airflow can prevent issues. Regular cleaning of the machine after use also helps maintain optimal performance levels.
– Common Issues and Solutions
Here are some frequent problems and their solutions:
- Inconsistent Arc: This may be due to incorrect voltage settings or dirty contacts. Ensure the machine settings are adjusted according to the material being welded, and clean all contact points.
- Poor Wire Feed: A common issue stemming from tangling or a feed issue. Check that the wire is correctly loaded and that there are no obstructions in the feed path.
- Excessive Spatter: Reducing the voltage or adjusting the wire feed speed can help mitigate this issue. Proper technique and maintaining a steady hand also contribute to better results.
– Tips for Effective Use of the Unimig Viper
Some pro tips for maximizing your experience with the Unimig Viper include:
- Practice using different settings on scrap material to understand how each setting affects performance.
- Use protective gear suitable for welding to ensure safety while working.
- Invest time in understanding different welding techniques for each process to enhance the quality of your work.
5. Customer Reviews and Comparisons
– What Users Are Saying about the Unimig Viper
Overall customer reviews highlight the Unimig Viper’s reliability, ease of use, and effectiveness across different welding processes. Users appreciate its lightweight design and compact size, which make it a convenient choice for both home and industrial applications. Several reviews echo sentiments around the good quality welds achievable right out of the box.
– Comparing the Unimig Viper with Other Welders
When compared to its competitors, such as the Unimig Razor series, the Viper series offers distinct advantages in portability and price point. While the Razor series might boast higher AMP capabilities, the Viper is more accessible for beginners and versatile for various projects. Evaluating features such as warranty options, user reviews, and additional support can guide potential buyers in making well-informed decisions.
– Conclusion: Is the Unimig Viper Right for You?
In conclusion, the Unimig Viper welder represents an ideal blend of versatility, performance, and user-friendliness. It caters to multi-process welding requirements, making it a valuable asset for both novice welders and experienced professionals. From its compact design to robust performance metrics, it’s evident that the Unimig Viper has been crafted with the user in mind, consistently delivering high-quality welding results across various tasks and environments.